
Posted October 17, 2019
MYRTLE BEACH, S.C. – Last month, I covered the venerable Southern Textile Research Conference (STRC) here and gleaned a number of takeaways. Among them:
What took me so long to attend this exceptional event?
Another:
Why don’t more professionals in our industry attend?
On the first point, why haven’t I covered the STRC in the past? Well, beyond the fact that it has often overlapped other events I deemed slightly more important, I thought it would be very technical and too much in the molecular weeds for a global audience. Yes, it was technical, but not entirely. It was also historically eye opening, with useful, awe-inspiring information for a wide swath of our amazing industry. Oh, and the networking was sensational – one of the primary reasons I cover so many events annually (going back to the “being present” mantra I’ve mentioned here before).
The STRC brings together academia and industry (always a good thing) to review the latest research, revolutionary breakthroughs and reports of our industry’s renaissance. Topics this year included dyeing and finishing, protection and comfort, performance textiles, digital printing and more.
The STRC, founded in 1961, has obviously changed with the times over the years, explained STRC Chairman Mike Leamon, global textile technology manager at Pulcra Chemicals, Rock Hill, S.C.
“The original format was only two presentations per day, and each presentation was two or two-and-a-half hours,” he said, in opening remarks to attendees. “In those days the speaker would talk for one to one-and-a-half hours and then there would be one to one-and-a-half hours of debate. And in those days, the debate wasn’t just with the speaker, but most of the time the debate was between attendees about what the solution to the problem was or what caused the problem or whatever. Over time, that changed. We still have a presentation of one hour, with about 15 minutes of debate. So this is still different from most conferences.”
From an historic standpoint, Preston Aldridge, sales engineer at FTA, Inc., Inman, S.C., bucked that recent trend and delivered the goods – and then some. In a two-hour, two-part, interactive talk, he presented, “Evolution of Chemical Applicators for Textiles – An Historical Review of Chasing Water.” And, man, I can understand why STRC organizers gave him the floor for two long segments. Aldridge went back in history – way back – all the way to Adam and Eve to cover the “water problem” in textiles.
After modesty emerged as a result of Eve’s first bite of the apple, he surmised that, “Adam discovered after the first laundry that it took six hours for his fig leave to dry when Eve wrung it. But it took Adam only three hours to dry because he could wring it harder than Eve.”
That kicked off a fascinating discussion about how the textile industry in the dyeing and finishing area evolved over the years. He plunged into how the industry has handled the “water issue,” outlining that it has had to “wring it out, pound it out, squeeze it out, spray it out, ‘kiss’ it out (with kiss rolls), ‘foam’ it out and ‘plasma’ it out.”
“That’s what my career has been about,” said Aldridge, who has more 58 years of experience in the industry. “Water is the most necessary thing in our industry that there ever was, because of the old rule that the secret to pollution is dilution. We had to dilute our chemicals because the solution is dilution. We had to dilute our chemicals because we didn’t know how to put them on if they weren’t diluted. We had to dilute our wastewater because we didn’t know what else to do with it to get the color out and the chemical concentration down. So we were a classic example of water hungry.”
Aldridge went on to discuss in detail the technological advances over the years that address the issue, all the way up to today’s foam and plasma solutions, interspersing personal and often humorous anecdotes about personal experiences with various methods.
On the latter, he explained that atmospheric plasma is sustainable, water-free and requires low-level chemistry.
“Plasma finally ends my career. The water is gone with this technology. So if I could find my replacement, I could retire,” he quipped. “Plasma gets water out of the industry. And that’s a tremendous thing. Is it for every application? Maybe not. I don’t know. But we didn’t think foams were for every application at one time, and we didn’t think sprays were for every application at one time. But they cover more territory today than they did when they first started.
“You’re living in an exciting time it this industry because things can change so incredibly fast now,” he continued. “You never know when the next evolutionary thing is going to happen in plasma.”
He went on to say that he helped eliminated water through applicators in his lifetime. But plasma, he added, “eliminates applicators, for gosh sakes. You put the chemistry in the way you make the fabric to begin with. I find that totally fascinating.”
In closing, Aldridge said, “What I would love for you to take away from this talk is to go back and apply the enthusiasm that whatever it is you’re working on that I still have for this industry. Somebody asked me, ‘why don’t you retire?’ I said, ’I did. I retired about 20 years ago. I sat down and tried to figure out what I wanted to do when I retired and I discovered I was already doing it. I have relationships with people, and the travel allows me to see my grandkids more than I would see them if I was sitting at home. I wouldn’t take anything for the opportunity this industry has offered me. Take some of that back and apply enthusiasm to whatever it is you’re working on that’s driving you nuts in your job. Enthusiasm opens up the pores in your brain, and with that, things might start clicking together a little bit better.”
Wow. Technical, but introspective and inspiring, too. Thank you, Preston, for such an inspiring talk.
Value-added finishing
Afterward, Don Alexander, president of Anovotek, LLC, Barnwell, S.C., discussed his company and capabilities in a presentation titled, “Value-Added Finishing in the USA: Strategies Enabling Innovation and Entrepreneurial Business Development.” Anovotek integrates performance materials into textiles, polymers and other products.
“Fabric finishing is economically viable in the U.S., but cut and sew is the difficult part,” he said. “We make fabrics cost effectively, but it’s hard to get the cutting and sewing, driven by the lack of labor. What we’re trying to do is take advantage of those changes in consumer shopping habits and couple that with a unique business model where we can sell value-added products through e-commerce and use global sourcing and garment finish goods in the U.S.”
Alexander talked about Anovotek’s strategy and provided technical details about its company operations.
“The textile industry has always followed the needle,” he said. “So sewing in the U.S. is very difficult because it’s very labor intensive. The lack of labor drives you to look outside the country.”
He then deep-dived into the state of retail and consumer purchasing trends and why those are important factors in his company’s business strategy. Its growth model, he said, is to offer variety and fashion through a global supply chain and to “unlock the digital potential of rural America” that has certain advantages for a small company and its customers, including performance attributes, low inventory requirements and speed to market.
“We’ve been doing this for 10-plus years,” Alexander said. “Orders arrive and within a week we can turn them into a performance retail product.”
Anovotek’s products, which include insect-repellant apparel, is available on Amazon (as an Amazon Choice product) and other online sources, he said.
“Year-over-year, some of these products are doubling and some even higher than that,” Alexander said. “So the opportunity is there. We’re taking a very fast-evolving sales environment, coupling it with something all of us know has been there for a long time, and just using it in a little bit different way: Source globally, treat in the U.S – which protects our I.P. and allows us to move fast – and put a high value add so we can sell this at a much higher premium, sell it direct to the consumer and bypass traditional retail. So it’s an interesting approach, a little different than what you’ll hear from a lot of people, but we think it has a lot of merit for people in the U.S.”
Textile protection and comfort
Dr. Roger Barker, director of the Textile Protection and Comfort Center (TPACC) and Burlington Distinguished Professor, Department of Textile Engineering, Chemistry and Science at N.C. State’s Wilson College of Textiles, offered an interesting presentation, “Evaluating Textiles with Performance Properties.”
TPACC, celebrating its 25th anniversary this year, is the only academic center in the U.S. that incorporates in one location the capabilities to research, test and evaluate the comfort and protective performance of textile materials, garments and ensemble systems. He discussed in detail how the center is equipping responders for challenges they’re facing – from the challenges of 9/11, to cancer in the fire service industry to wildfires out West.
The info imparted and the associated videos were all fascinating and important.
Water, water everywhere
Also, Tim Heller, vice president and plant manager at JB Martin, discussed, “A Novel Approach to Dyeing Cotton Using Foam.” He went over the need for water, global areas experiencing water shortages, how pollution exacerbates the problem and textile dyeing pollution.
More than a half trillion gallons of fresh water are used in the dyeing process of textiles each year, he said. And in India and Bangladesh, dye wastewater is discharged, often untreated, into nearby rivers, eventually spreading into the sea.
“Reports show a dramatic rise of diseases in these regions due to the use of highly toxic discharges,” he noted. “In China, the world’s largest clothes exporter, the State’s Environmental Protection Administration declared that nearly one third of the country’s rivers are too polluted for direct human contact.”
Heller mentioned how he has benefited from attending the STRC for 20 years, which led him to work with Aldridge, Gaston Systems and Cotton Incorporated on dyeing trials.
“We had the a-ha moment in 2009 working with Ken (Greeson) at Cotton Inc.,” he said. “We felt like we had something special and something important with this. We thought we were close but we didn’t quite have the process. Now, how can we commercialize it? How do we make it relevant for as many people as we can?”
He then went into the Oasis Process of foam-based precision application of dyeing through a Gaston Systems CFS® dye application system on a modified cellulosic substrate (cotton, rayon or linen), which is then fixed in an environment that permanently attaches the dye to the substrate with little or no after-washing.
The Oasis fabric preparation modifies the cellulosic substrate, changing it from being negatively charged to being positively charged, he reported. This is done during the fabric preparation step and requires the addition of Oasis Reagent using either pad batch or pad steam, he added.
The benefits, Heller said, is 85 percent less water required with effluent limited to system cleaning water of approximately 150 l/color; almost 100 percent dye utilization; 60 percent reduction in energy and CO2 emissions; efficiency, even with short lots; a small machine footprint; and labor savings.
“I think we’re only scratching the surface with this,” he said.
Other speakers
On the digital printing front, Katelyn Lee, specialty applications chemist at Cotton Incorporated, covered advancements in digital printing machinery, sharing some of the new technologies she witnessed at ITMA in Barcelona in June. Her presentation included a history of digital printing, the current state of the market, machinery developments, print head developments, new applications, business developments and more.
Also, David Clark, Ink Jet Textiles, Huntsman Textile Effects, went over advancements in digital printing inks and chemistry.
And keynoter Diana Wyman, new executive director of the AATCC, gave an overview of her global association while also discussing global testing and standards for the textile industry. She talked about global challenges in developing standards for a diverse global audience.
Postscript
Oh, and to my second question asked above: Why don’t more professionals in our industry attend? I can’t answer that, being a newbie. But I do know that from talking with Mike Leamon and Ken Greeson that, at one time, this conference was strictly technical personnel and was by invitation only. And attendees changed over the years and evolved to include a balance of technical personnel from industry/manufacturing, textile suppliers and textile university professors.
My goal for next year is to promote the heck out of this conference and invite all of my readers to attend. You won’t be disappointed.
![]() |
---|
![]() |
![]() |
![]() |
![]() |
![]() |
![]() |
![]() |
![]() |
![]() |
![]() |
![]() |
![]() |

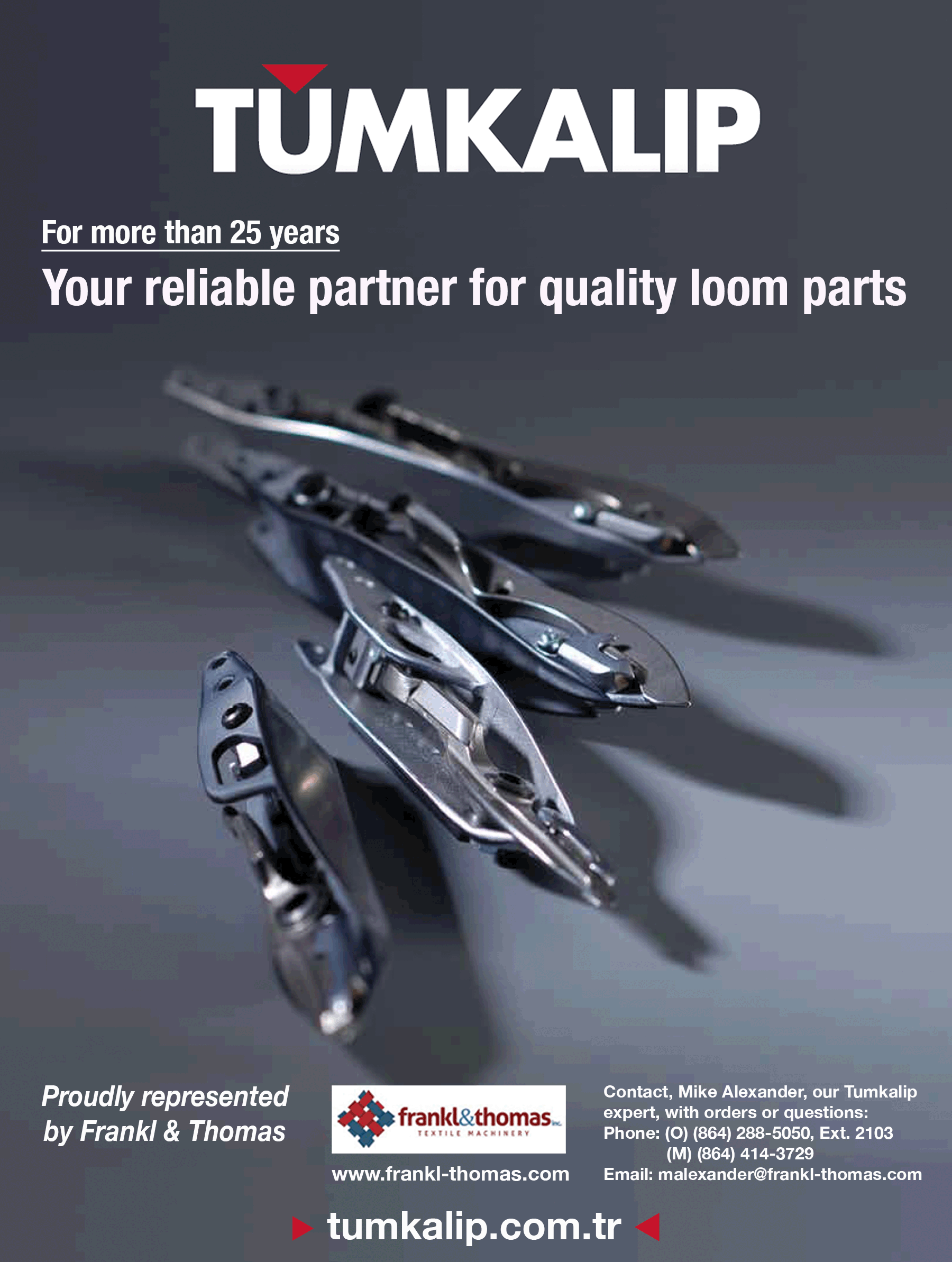
Previous blog posts
• STA Marketing Forum keeps rockin', y'all (October 9, 2019)
NCTO Fiber Council members gain insights at Fall Meeting (September 26, 2019)
• AAPN's 'Dynamic Duo' honored (July 18, 2019)
• AAPN again helps connect the dots with ‘Carolina Mill Express’
• Women in Textiles Summit inspires ALL (April 18, 2019)
• STA Summer Marketing Forum a grand slam (October 4, 2018)
• No ordinary Joe (September 6, 2018)
• Opioid crisis hits home for textile leader and family (August 30, 2018)
• Martin Foil was a powerful, longtime voice in the industry (August 9, 2018)
• SYFA REVIEW: What's giving fibers and textiles a bad name now? (July 12, 2018)
• Disruption: An apropos buzzword at AAPN event (June 28, 2018)
• AAPN's Carolina Mill Tour blowing minds (April 12, 2018)
• Super-sized superlatives (February 1, 2018)
• Textile industry is Jim-dandy (January 18, 2018)
• SEAMS poised to build U.S. supply chain bridge (December 6, 2017)
• Endless gratitude (November 22, 2017)
• Allen Gant Jr.: In his own words (October 12, 2017)
• Mark Kent: Another good guy gone too soon (August 25, 2017)
• WIth grace and humility, Chapman made the world a better place for alll (August 29, 2017)
• Time moves, even in textile time (August 2, 2017)
• Technology driving trade show trends (July 12, 2017)
• Let's get ready to RUMMMBLE! (June 7, 2017)
• Themes, talking points from 10 weeks of travel (June 1, 2017)
• Chesnutt: Champion, statesman, friend to all (May 4, 2017)
• To Witt: A big thank you (April 27, 2017)
• Rebranding textiles, one mind at a time (April 5, 2017)
• Thrills on the Hill (March 23, 2017)
• Don't mess with textiles (March 9, 2017)
• Two steps forward, one step back (February 28, 2017)
• The industry spoke, N.C. State listened (February 23, 2017)
• Everybody knows Gabe (February 16, 2017)
• Tantillo still standing tall (February 1, 2017)
• Here's what I'm hearing (January 18, 2017)
• Inside the colorful mind of Alexander Julian (January 4, 2017)
• Kimbrell, Warlick dynamic served Parkdale well (December 15, 2016)
• Vanguard's Wildfire: Sparking a revival? (December 7, 2016)
• A hearty serving of gratitude (November 30, 2016)
• Steve Brown's legacy endures (November 17, 2016)
• Chastain helped lead industry's good fight (November 9, 2016)
• Calendar conflicts cause consternation (October 12, 2016)
• Summer rocked; fall equinox knocks (September 21, 2016)
• Calling all 'texvangelists' (August 31, 2016)
• U.S. textile industry's summertime roar (August 24, 2016)
• Staying front and center as manufacturing resource (August 9, 2016)
• Media 'amazement' (August 4, 2016)
• A phoenix-rising day (July 20, 2016)
• Inman Mills, SCMA helping to build 'workforce of the future (July 12, 2016)
• STA joins fab 500 club (June 23, 2016)
• Spring postscript: Energy, enthusiam, excitement (June 15, 2016)
• What I'm seeing and hearing (May 18, 2016)
• Notes from the road (May 2, 2016)
• What a week for U.S. textiles (April 20, 2016)
• Zooming, zipping and zigzagging (April 6, 2016)
• Bring it on(shore) (March 23, 2016)
• A Bell-ringing experience (March 9, 2016)
• Not your average Joe (February 23, 2016)
• The X(clusive) factor (February 16, 2016)
• Where are they now? (February 10, 2016)
• Being a little better (February 2, 2016)
• A seat at the table (January 27, 2016)
• Mind the skills gap (January 20, 2016
• Hitting the jackpot (January 12, 2016)
• Let's resolve to ... (January 6, 2016)
STRC: Venerable group does deliver the goods