
Posted May 8, 2019
THE CAROLINAS – Last month, I rode a bus with 24 (mostly) young people from a dozen brands and organizations through the highways and byways of the two Southern sister states. We were on the Americas Apparel Producers Network’s (AAPN’s) “Carolina Mill Tour Express” (my term), the second iteration of this unique journey that took us to seven textile facilities in six days.
Oh, and somehow, we were able to squeeze in a half-day educational event, AAPN’s Charlotte Regional Conference, where Barbara Zeins, president of Gerson and Gerson, Inc., and Tom Glaser, vice president at VF Corporation and president of its supply chain, imparted extensive knowledge from their years of experience in our industry.
The tour started last year at the behest of Ron Roach, president of Contempora Fabrics, to help brands who work with textile producers better understand the processes it takes to make their raw materials, as well as the terminology, the testing and the techniques it takes to make a yarn, a fiber or a fabric. Or, as Tony Anzovino, chief sourcing & merchandising officer, Haggar Clothing Co., Dallas, has said of one of his goals as president of AAPN, he wants the network to grow “AIQ” (Apparel Intelligence Quotient). He has described AIQ as a person’s proficiency in, or knowledge of, the apparel and textile industry.
Those objectives were clearly accomplished, especially when you read the feedback from below from a few participants. And if you witnessed them taking many, many photos with their cell phones and asking inquisitive, well-thought-out questions, you know they were eager to learn and grasping the information imparted.
This year, attendees received tours and a few hands-on workshops at: Contempora Fabrics, Lumberton, N.C.; Patrick Yarns/Coats, Kings Mountain, N.C.; Milliken’s Innovation Center in Spartanburg, S.C., and its Magnolia Finishing plant in Blacksburg, S.C.; Carolina Cotton Works (CCW), Gaffney, S.C.; Parkdale’s W. Duke Kimbrell Plant, Gaffney, S.C.; Hamrick Mills, Gaffney, S.C.; and American & Efird (A&E), Mount Holly, N.C.
Here are what some of the tour takers said:
Miranda Tidwell, materials developer, Supply Chain, VF Workwear, Nashville, Tenn.:
“This is a great experience! It was worthwhile to take time to concentrate on manufacturing processes. I made meaningful contacts both at the mills and with fellow tour participants.
“CCW and Parkdale clearly outlined the processes before we got into the plants. The small tour group sizes encouraged us to ask questions. The automation at Parkdale was impressive. Details of sustainability efforts at A&E and Parkdale were enlightening. I usually hear efforts explained in broader terms.”
-----------------------
Avery Davis, production manager, Haggar Clothing Co., Dallas:
“Overall, I was very impressed with the content of the tours. Most were very interactive and I learned a lot. I appreciated the variety of businesses featured on the tour. The speakers and tour guides were very knowledgeable.”
Asked what stood out, she answered, “Parkdale and their innovation with automation. And I learned that regular household items can be turned into fabric. I also noticed most of the business on the tour had sustainability initiatives. I wasn’t privy how important sustainability was to the businesses goals.”
She added: “I work in sourcing (specifically production) so learning about this pivotal part of the supply chain will help me make more informed decisions.”
-----------------------
Dorota Arcentales, fabric manager, PVH, New York City:
“My general impressions are that the tours were very well organized, and I love that we were able to experience such a wide breadth of plant specialties – from knitting to yarn spinners to dye house and even a thread spinner! Our schedules were quite on point – just the right amount of touring/learning and socializing with the mill partners and other tour members, any more would have been overwhelming, any less would have been disappointing. It was a perfect combination.”
She added that she was “completely blown away” by Parkdale. “The fact that the plant was almost entirely automated was something I have never seen before, and the robots driving around the plant performing tasks was really eye-opening. I felt that the facility was extremely clean, well maintained and the workers that were there seemed happy and friendly with each other. I also love that everything was recycled – cotton waste was donated to local farmers and even finer waste from cotton waste was compacted into food for rodeo bulls in S.C. It really showed the sense of partnership with the people and that this plant gives back to its community. I loved that.
“Another thing I found very impressive was the president’s (Charles Heilig’s) forward-thinking and vision for the future of the plant. He seemed very passionate about the industry, the people that work for the plant and sustainability and he seemed to be on top of the topic of automation and AI and what it means for his plant in the years to come. I feel Parkdale should stand as an example for other facilities in this industry. They do a fantastic job.”
Arcentales also said that, “quite honestly, most of the things I’ve learned I wasn’t aware of it – I acquired such a wealth of information on this tour that I don’t even know where I would start to be able to cover everything.”
But she did mention: a) Most facilities treat the waste water from the plant and by the time it leaves the plant to go back to the local water system, it is cleaner than when it came in; b). the advancements in automation taking place in the U.S. mills and how much further they are than I had thought; c) that the U.S. textile industry is well and still thriving despite so many challenges of offshoring and lack of labor force and how there are so many individuals passionate about what they do and they work hard to keep the U.S. business going. So inspiring!
“I think most U.S. companies only send their associates to similar (but not even close) educational/business trips overseas, and most of us do not get the chance to experience how this industry looks like on our continent, where it is now and where it originally came from and what is being done to keep the momentum going and advance the business here,” she continued. “I would say it should be mandatory for all raw materials professionals in the U.S. to visit the plants here and have a chance to network and maybe even try to do business with these amazing, inspiring companies. There are so benefits to buying raw materials in the U.S. that I feel will offset any challenges on cost more and more, with the advancements in technology, in the years to come.”
-----------------------
Elizabeth Back, Supply Chain Development, VF Workwear, Nashville, Tenn.:
“Some very impressive work for the apparel/textile industry is being completed essentially in our own backyard. It was wonderful to see so many excellent companies employing so many wonderful people and manufacturing in the U.S. Tours were very informative and educational. As odd as it may sound, I was very impressed with how clean the mills were. I have been to other domestic mills that were nowhere near the cleanliness of the mills we visited.”
She added: “I was very impressed with Contempora, CCW and Parkadale. I have never been to a mill that manufactures yarn and this was a new and exciting experience for me. I was amazed by the detail, technology and automation Parkdale brings into manufacturing. CCW and Contempora knock quality and process out of the park! Contempora’s educational sessions were very helpful to understand the basic of textiles, quality and the manufacturing process.”
She also said that yarn manufacturing is a whole new arena for here. “While I understood the basics, I had never been to a yarn manufacturing facility before and the processes/steps to take a fiber and turn it into a functional yarn was extremely impressive.”
Grading the event overall, the added: “The Carolina Mill Tours would be very helpful and eye opening to pretty much anyone in the apparel market who is responsible for developing, producing, planning or sourcing goods. It was helpful to see all the steps in the fabric manufacturing process from fiber level, to yarn level, to spinning and knitting and then dyeing and finishing. It really is a process! Our end-users and customers often wonder why the development process is so long, you can see why on the tour! It is also very helpful making industry connections and learning about new sources/resources. I thoroughly enjoyed meeting all the new people!”
-----------------------
Felipe Antunez, color coordinator, Fanatics LATAM, Honduras:
“Personally I learned a lot of new technical things that can be apply to my day-to-day activities. Sue (Strickland) and Mike (Todaro) make a great job organizing the event.
“Parkdale was amazing,” he added. “I couldn’t believe how automated their facility is. Hamrick was great, too. It is the first time I visited a woven mill. Woven knitting and the dyeing process were new for me. And the Contempora Fabrics session with Alex (Whiteley) was great.
------------------------
Leslie Cook, manager, Product Integrity Safety/Quality Compliance, Fanatics, Tampa, Fla.:
“Overall, I was very pleased with the tour. The tour is a great learning tool for those new to this part of the industry, and it’s a great refresher. One girl called it a ‘crash course,’ and I do agree. I would absolutely do it again. Companies such as Parkdale, Contempora, CCW, A&E, Hamrick – they did a great job. We learned there, we had little ‘ah-ha’ moments and physical takeaways to reference later from home.
“I was especially impressed watching (employee) Nancy at Contempora manually repairing damages from the knitting process,” she added. “And I was impressed with the entire cotton process at Parkdale, starting from the cotton fluff to ending in yarn and fabric. The same thing for woven fabrics at Hamrick – I’ve seen knitting before, but they were my first woven facility. It was so cool to see that in person.”
Commenting on the overall experience, Cook added: “As a quality manager, I feel it is imperative to understand how your suppliers operate from start to finish. Quality starts at the beginning of the cycle; it should never be an afterthought. These tours are a great learning tool to see how things are done in general (cleaning cotton, knitting, dyeing) but it’s particularly helpful, and rather interesting, to see how suppliers do things differently. Whether they rely on automation (robots) and software or still rely on lots of manual processes; whether they’ve developed their own software or equipment, or perhaps purchased software with the agreement to modify and customize as needed. It was nice to see the housekeeping at each facility (is lint floating everywhere or is it controlled?). And hearing how each company treats its workers; what are the shifts like, how much time off, health checks, etc. It’s important to understand all challenges your suppliers face and strides taken to achieve their goals.”
-----------------------
Meagan A Cowles, materials developer, Supply Chain, VF Workwear, Nashville, Tenn.:
“Overall the mill tour was great. I was able to take something away from each stop and figure out a way to apply it to my daily role at VF. I walked away feeling empowered and excited about this industry.
“I currently work with Contempora and most of my fabrics they knit are finished at CCW,” she continued. “I enjoyed seeing how the two mills operated. This gives me a better understanding of any quality issues that I may see from a fabric standpoint. I can now fully understand at what process the issue occurred.
“A&E was a great learning experience,” she added. “I never really thought about how the sewing thread is what holds everything else together. For instance, you can have a great fabric and garment construction, but if you don’t use the correct thread, you are taking a risk. That was an aha moment for me!
"Most of my career has been in knits, I am just now digging deep into woven fabrics. Seeing all the work that goes into setting up a woven fabric and creating the warp was a game changer for me. The woven process is starting to make more sense and I have a deeper appreciation for each fabric construction. I was not aware of the government checking the cotton and giving it a rating, so yarn mills can blend the different qualities. Parkdale commits to having a consistent cotton yarn for 52 weeks, meaning that each yarn should dye in a consistent fashion for 52 weeks. I also now understand why woven mills having higher MOQ if they are a continuous dying manufacture.”
Cowles added that the best part was being around passionate people – “people who want to learn and grow, seeing someone’s face the first time they walk into a plant. Unfortunately, you don’t see this type of passion every day in the office. Since this tour, I view my role in a different light. I now have a better understanding of the overall supply chain and even more of an appreciation for the hard-working manufacturers that make this industry possible. I’m very grateful for the experience!”
-----------------------
Dilshan De Silva, senior manager, Western Hemisphere Sourcing, Global Communications & Product Integrity, Jockey International, Inc., Kenosha, Wis.:
“Overall, It was an educational, insightful and enjoyable week. What stood out for me was Contempora Fabrics, Carolina Cotton Works and Parkdale mills. I loved the presentations, classroom physical experiments, take-away materials and organized easy to follow facility tours they put together.
“It was good to see how much these U.S. plants have developed, and the technological advancement investments that some of these plants have made. It gives us insights to broader options available in the U.S. itself. As speed becomes vital in today’s business, this opens up more ways for us to think of what we can do closer to our markets.”
He concluded: “It gives an opportunity to learn some of the intricate parts of the manufacturing operations of each component and understand operational challenges and opportunities. Also, it was a great opportunity to interact and discuss with senior executives in respective facilities we visited as well as with fellow participants on our operational challenges and exchange knowledge/ideas. I’m sure these relationships we built with each other will continue way beyond the week we had together.”
-----------------------
Jill Loughridge, fabric assistant, Dick’s Sporting Goods, Coraopolis, Pa.:
“Overall, I was really pleased with the tour. The mills seemed genuinely interested in educating all of us! Parkdale’s spinning was really impressive to me. I was amazed by the automation that they use in their facility.
“I didn’t realize how technologically advanced some of the region’s products are,” she added. “Discussing the specialty yarns for end uses like military protection and airline carpets was so fascinating.”
She added that “being more educated with the process will help us do what’s right for our company. For example, seeing that dye lots are handled by weight could be useful in MCQ negotiations when needed. Also, seeing the quality of the products and working conditions sets a great standard for us as we visit other mills around the globe. And maybe most importantly, it was absolutely wonderful to meet so many industry peers and discuss our common challenges.”
AAPN again helps connect the dots with ‘Carolina Mill Express’
Previous blog posts
• Women in Textiles Summit inspires ALL (April 18, 2019)
• STA Summer Marketing Forum a grand slam (October 4, 2018)
• No ordinary Joe (September 6, 2018)
• Opioid crisis hits home for textile leader and family (August 30, 2018)
• Martin Foil was a powerful, longtime voice in the industry (August 9, 2018)
• SYFA REVIEW: What's giving fibers and textiles a bad name now? (July 12, 2018)
• Disruption: An apropos buzzword at AAPN event (June 28, 2018)
• AAPN's Carolina Mill Tour blowing minds (April 12, 2018)
• Super-sized superlatives (February 1, 2018)
• Textile industry is Jim-dandy (January 18, 2018)
• SEAMS poised to build U.S. supply chain bridge (December 6, 2017)
• Endless gratitude (November 22, 2017)
• Allen Gant Jr.: In his own words (October 12, 2017)
• Mark Kent: Another good guy gone too soon (August 25, 2017)
• WIth grace and humility, Chapman made the world a better place for alll (August 29, 2017)
• Time moves, even in textile time (August 2, 2017)
• Technology driving trade show trends (July 12, 2017)
• Let's get ready to RUMMMBLE! (June 7, 2017)
• Themes, talking points from 10 weeks of travel (June 1, 2017)
• Chesnutt: Champion, statesman, friend to all (May 4, 2017)
• To Witt: A big thank you (April 27, 2017)
• Rebranding textiles, one mind at a time (April 5, 2017)
• Thrills on the Hill (March 23, 2017)
• Don't mess with textiles (March 9, 2017)
• Two steps forward, one step back (February 28, 2017)
• The industry spoke, N.C. State listened (February 23, 2017)
• Everybody knows Gabe (February 16, 2017)
• Tantillo still standing tall (February 1, 2017)
• Here's what I'm hearing (January 18, 2017)
• Inside the colorful mind of Alexander Julian (January 4, 2017)
• Kimbrell, Warlick dynamic served Parkdale well (December 15, 2016)
• Vanguard's Wildfire: Sparking a revival? (December 7, 2016)
• A hearty serving of gratitude (November 30, 2016)
• Steve Brown's legacy endures (November 17, 2016)
• Chastain helped lead industry's good fight (November 9, 2016)
• Calendar conflicts cause consternation (October 12, 2016)
• Summer rocked; fall equinox knocks (September 21, 2016)
• Calling all 'texvangelists' (August 31, 2016)
• U.S. textile industry's summertime roar (August 24, 2016)
• Staying front and center as manufacturing resource (August 9, 2016)
• Media 'amazement' (August 4, 2016)
• A phoenix-rising day (July 20, 2016)
• Inman Mills, SCMA helping to build 'workforce of the future (July 12, 2016)
• STA joins fab 500 club (June 23, 2016)
• Spring postscript: Energy, enthusiam, excitement (June 15, 2016)
• What I'm seeing and hearing (May 18, 2016)
• Notes from the road (May 2, 2016)
• What a week for U.S. textiles (April 20, 2016)
• Zooming, zipping and zigzagging (April 6, 2016)
• Bring it on(shore) (March 23, 2016)
• A Bell-ringing experience (March 9, 2016)
• Not your average Joe (February 23, 2016)
• The X(clusive) factor (February 16, 2016)
• Where are they now? (February 10, 2016)
• Being a little better (February 2, 2016)
• A seat at the table (January 27, 2016)
• Mind the skills gap (January 20, 2016
• Hitting the jackpot (January 12, 2016)
• Let's resolve to ... (January 6, 2016)
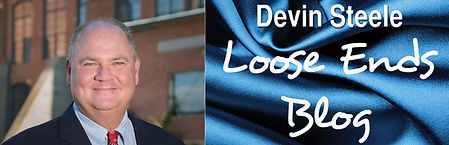
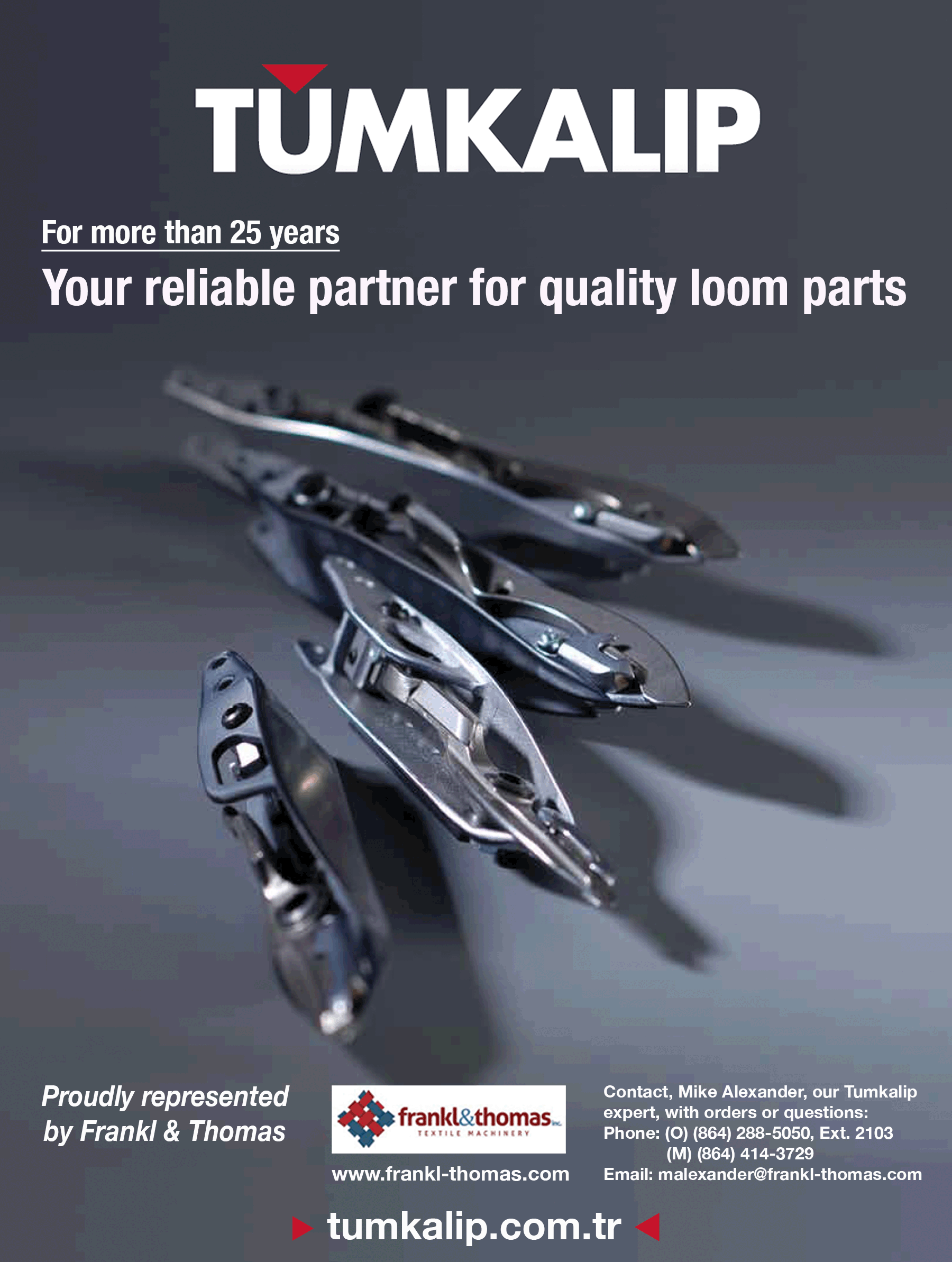
