
Posted March 26, 2020
If you’ve been paying any attention while self-isolating, you know it has become something of a wild wild West out there, at least in the world of Personal Protective Equipment (PPE). Every day (hourly, it seems) another company has jumped into the production or supply of materials to this space at a critical, unprecedented time for all.
While many of us have gotten out of Dodge and retreated to our home offices and Zoom Rooms during the COVID-19 crisis, a whole segment of our amazing industry has dropped everything at the spur of the moment to respond to the need for protective supplies for healthcare professionals, first responders and others.
Which makes me about as proud as I’ve ever been of you textile and apparel angels. As far as the eye can see, I’m witnessing good news of your good deeds and goodwill.
I’ve spent much of my time over the last week or so trying to lasso in all of these inspiring stories and connect people throughout the supply chain who want to get involved. I’ve had fiber producers, fabric makers, equipment dealers, chemical providers, media, a New York podcast producer organizing a webinar and even a doctor from the Cleveland Clinic contact me with questions related to this supply-and-demand conundrum. And I’m sure this has consumed many of you, as well.
Hardworking healthcare professionals around the country and the world have vociferated from behind their weariness their need for goods and equipment to keep them safe and healthy. And many of you stepped up in response, the Defense Production Act be damned. Hence, it’s become something of a benevolent free-for-all in this new frontier, leading to more questions than answers, especially around face masks.
And I’ve heard many of those questions: Where do they fall on the ASTM protection scale? Do they need FDA-approval? Are there harmonized standards? What are they made of? What are the specs? How do you make them? Where do you ship them? Who makes the elastic bands? Any antimicrobial or anti-viral ingredients? What is the quality? And on and on.
Fortunately, several companies and groups in our industry have come forth to help answer these questions and solve a number of issues. The Americas Apparel Producers Network (AAPN) on Sunday set up a Sourcing Center on its website that has attracted thousands of users connecting on the PPE issue. The AAPN also reached out to other associations, including the Industrial Fabrics Association International (IFAI), the American Apparel & Footwear Association (AAFA), SEAMS and others, to ask if they would invite their members to participate. All graciously obliged, according to AAPN leaders Sue Strickland and Mike Todaro.
And the IFAI, in conjunction with the National Council of Textile Organizations (NCTO) and INDA, Association of the Nonwoven Fabrics Industry, conducted a member survey to develop a list of suppliers of medical PPE for the government in light of the crisis. Response was overwhelming – from members and nonmembers. As a result, those groups are in the process of identifying specific government recipients such as officials at the Department of Health and Human Services, FEMA, the Department of Commerce, the Defense Logistics Agency and the White House itself to garner the greatest impact and benefit of the survey as possible. The goal is to ask the federal government to use the survey results to help inform sourcing decisions related to the emergency medical textile materials they are seeking to procure, according to Steve Schiffman, IFAI’s president & CEO.
And working with IFAI, NCTO, INDA and the Manufacturing Solutions Center in Conover, N.C., SEAMS developed a program to provide open capacity to help manufacturers in need where their own factories were closed or could not meet production requirements. Response to that program also has been overwhelming, according to SEAMS Executive Director Will Duncan.
Yarn spinner Parkdale, at the behest of the NCTO after the council was contacted by Peter Navarro, director of U.S. Trade and Manufacturing Policy, led a collaborative effort with eight other textile companies and apparel brands to build a supply chain “virtually overnight” and fast-track the manufacturing of medical face masks to help hospitals, healthcare workers and citizens battling the spread of the COVID-19 disease. Other companies have since joined the partnership.
That alliance appears to be the largest and most organized – it has certainly received the most national press in the U.S. – but numerous other production endeavors have popped up around the country. I’ve even seen several reports of others on an individual basis (seamstresses, for instance) volunteering to help produce PPE.
Another group of manufacturers and nonprofits, led by the Carolina Textile District (CTD), is transitioning its production to prototype and produce medical PPE supplies in response to a request from healthcare providers. On Monday, CTD launched a link on its website to handle intake of demand from healthcare providers and response from manufacturers that are willing to assist in the production process and provide supplies. In one day, more than 60 manufacturers signed on to help. In total, more than 600 sewers are available and ready to produce.
Equipment makers and suppliers such as Shima Seiki, Henderson Sewing Machine Co. and Belgium-based Reifenhäuser Reicofil also have adjusted their focus to healthcare PPE in the last week or so.
‘Never underestimate the power of the U.S. textile industry’
I contacted a few of those individuals whose companies are participating in these purpose-driven efforts to see how they’re doing. And several were gracious enough to come up for air, despite working virtually around the clock these days.
Among them was Jordan Schindler, CEO of Textile-Based Delivery, Inc. (Texdel), Inc./Nufabrx, who last week turned his Conover, N.C.-based company’s focus from medicated fabric for socks, compression sleeves, gloves and workout clothing to antibacterial face masks.
“We’re all just trying to do our part, but it’s been amazing to see how the whole industry has chipped in and banded together,” said Schindler, whose company is infusing fiber from Fiber & Yarn Products in Hickory, N.C., for production at partner Bossong Medical in Asheboro, N.C. “The offers for support have been amazing. It feels like everyone is banding together and going to war together.”
Already, the partners have begun shipping masks to hospitals while antimicrobial and air permeability testing continues at the Manufacturing Solutions Center, where Texdel/Nufabrx is housed.
“We are prioritizing delivery to hospitals and first responders, but doing what we can to help our local community as well,” Schindler said. “Masks will be going out to Catawba County first responders starting on Friday.”
Contempora Fabrics, a Lumberton, N.C.-based knitter, is part of the Parkdale coalition. Last Friday, the company’s finished quality manager created a few samples and, already, the manufacturer is producing 8,000 to 10,000 masks a day utilizing a medical customer that was already making them, as well as local plants.
“Next week we expect that capacity to double and continue to grow,” said Ron Roach, Contempora president. “It has been amazing to watch our industry come together to provide needed supplies quicker than anyone in the world could do. The entire industry in the U.S. and Western hemisphere is working on this as one big team. Never underestimate the power of the U.S. textile industry when it is called into action.”
LACorp of Lebanon, Va., was asked to join the Parkdale-led collaboration to provide cut-and-sew services. After spending the week on education and setting up supply chains, the company was running a small line producing a few thousand masks by today. Next week, it will add capacity, according to Jeoff Bodenhorst Jr., company president.
“We have committed to allocating labor for 25,000 or more of these antimicrobial-treated masks per week,” he said. “We are also assisting with approximately 50,000 gowns over the next few weeks.”
And because of the sudden shift, demand has quickly outpaced the supply of labor at LACorp, he added.
“We went from a period not two weeks ago where I was losing customer orders and extremely worried about my business to now maybe needing to hire staff to keep up with demand and ongoing opportunities,” Bodenhorst said. “Through networking with SEAMS, AAPN, the CTD (Carolina Textile District) and many other associations, my email box has blown up and I cannot get back to everyone quick enough. All the while we are educating employees, enhancing our cleaning protocol and getting everyone to practice social distancing.”
The silver lining to this whole health crisis? “The domestic sewn product supply chain pulling together to share resources and get something done in such a short period of time,” he said. “I hope this continues to draw attention to the importance of a domestic supply chain for many industries.”
Indeed, Bodenhorst brings up a bigger issue – but I’ll save that for another blog, once we all emerge from this cloud.
In the meantime, thank you for stepping up and proving our industry’s resilience, resolve and relevance. Your goodwill has not gone unnoticed.
Yippee ky-yay, y’all.
The wild wild West of PPE production
Previous blog posts
• Coronavirus wreaking havoc on textile events, much more (March 14, 2020)
• A heaping helping of thank-yous (November 27 2019)
• Cut and sew important – in textiles and in heart surgery (November 14, 2019)
• Venerable STRC delivers the goods (October 17, 2019)
• STA Marketing Forum keeps rockin', y'all (October 9, 2019)
NCTO Fiber Council members gain insights at Fall Meeting (September 26, 2019)
• AAPN's 'Dynamic Duo' honored (July 18, 2019)
• AAPN again helps connect the dots with ‘Carolina Mill Express’
• Women in Textiles Summit inspires ALL (April 18, 2019)
• STA Summer Marketing Forum a grand slam (October 4, 2018)
• No ordinary Joe (September 6, 2018)
• Opioid crisis hits home for textile leader and family (August 30, 2018)
• Martin Foil was a powerful, longtime voice in the industry (August 9, 2018)
• SYFA REVIEW: What's giving fibers and textiles a bad name now? (July 12, 2018)
• Disruption: An apropos buzzword at AAPN event (June 28, 2018)
• AAPN's Carolina Mill Tour blowing minds (April 12, 2018)
• Super-sized superlatives (February 1, 2018)
• Textile industry is Jim-dandy (January 18, 2018)
• SEAMS poised to build U.S. supply chain bridge (December 6, 2017)
• Endless gratitude (November 22, 2017)
• Allen Gant Jr.: In his own words (October 12, 2017)
• Mark Kent: Another good guy gone too soon (August 25, 2017)
• WIth grace and humility, Chapman made the world a better place for alll (August 29, 2017)
• Time moves, even in textile time (August 2, 2017)
• Technology driving trade show trends (July 12, 2017)
• Let's get ready to RUMMMBLE! (June 7, 2017)
• Themes, talking points from 10 weeks of travel (June 1, 2017)
• Chesnutt: Champion, statesman, friend to all (May 4, 2017)
• To Witt: A big thank you (April 27, 2017)
• Rebranding textiles, one mind at a time (April 5, 2017)
• Thrills on the Hill (March 23, 2017)
• Don't mess with textiles (March 9, 2017)
• Two steps forward, one step back (February 28, 2017)
• The industry spoke, N.C. State listened (February 23, 2017)
• Everybody knows Gabe (February 16, 2017)
• Tantillo still standing tall (February 1, 2017)
• Here's what I'm hearing (January 18, 2017)
• Inside the colorful mind of Alexander Julian (January 4, 2017)
• Kimbrell, Warlick dynamic served Parkdale well (December 15, 2016)
• Vanguard's Wildfire: Sparking a revival? (December 7, 2016)
• A hearty serving of gratitude (November 30, 2016)
• Steve Brown's legacy endures (November 17, 2016)
• Chastain helped lead industry's good fight (November 9, 2016)
• Calendar conflicts cause consternation (October 12, 2016)
• Summer rocked; fall equinox knocks (September 21, 2016)
• Calling all 'texvangelists' (August 31, 2016)
• U.S. textile industry's summertime roar (August 24, 2016)
• Staying front and center as manufacturing resource (August 9, 2016)
• Media 'amazement' (August 4, 2016)
• A phoenix-rising day (July 20, 2016)
• Inman Mills, SCMA helping to build 'workforce of the future (July 12, 2016)
• STA joins fab 500 club (June 23, 2016)
• Spring postscript: Energy, enthusiam, excitement (June 15, 2016)
• What I'm seeing and hearing (May 18, 2016)
• Notes from the road (May 2, 2016)
• What a week for U.S. textiles (April 20, 2016)
• Zooming, zipping and zigzagging (April 6, 2016)
• Bring it on(shore) (March 23, 2016)
• A Bell-ringing experience (March 9, 2016)
• Not your average Joe (February 23, 2016)
• The X(clusive) factor (February 16, 2016)
• Where are they now? (February 10, 2016)
• Being a little better (February 2, 2016)
• A seat at the table (January 27, 2016)
• Mind the skills gap (January 20, 2016
• Hitting the jackpot (January 12, 2016)
• Let's resolve to ... (January 6, 2016)

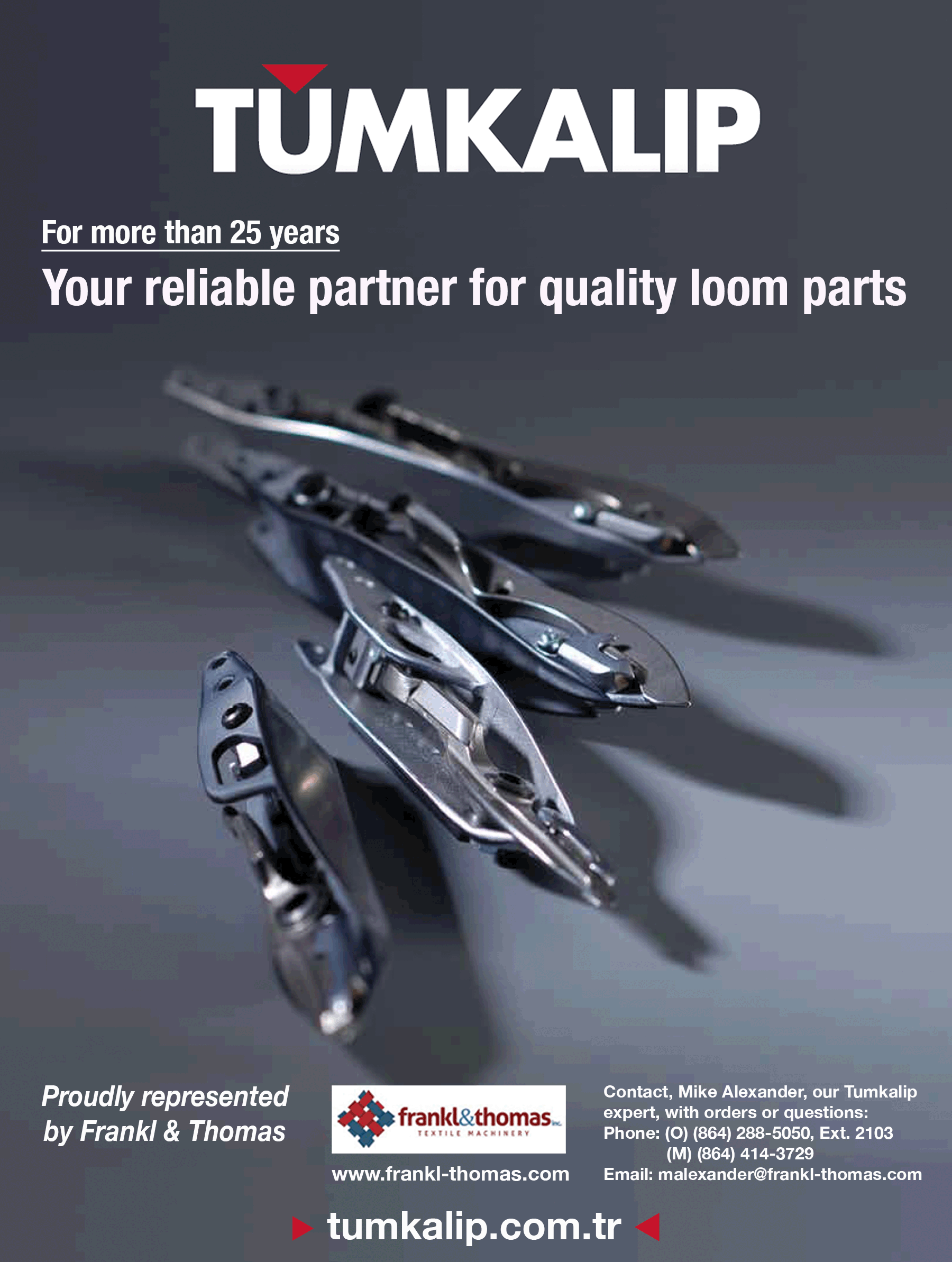
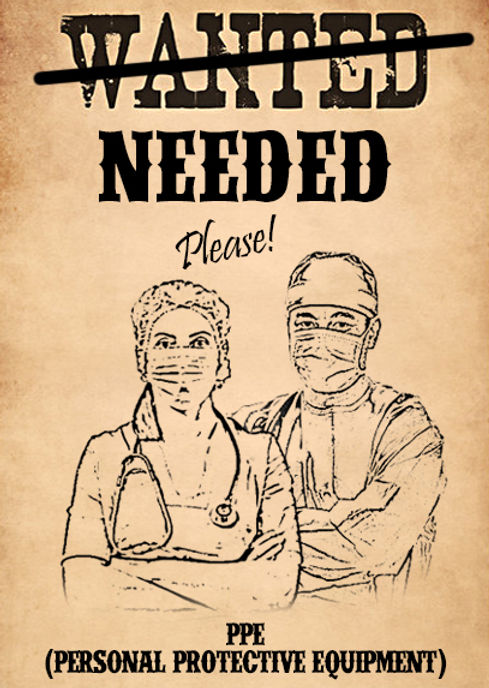
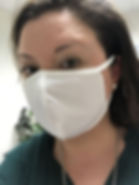
These face masks were knitted this week by Contempora Fabrics in Lumberton, N.C. Contempora is one of more than a dozen companies involved in the Parkdale-led collaboration to produce the needed PPEs.

These face masks were knitted this week by Contempora Fabrics in Lumberton, N.C. Contempora is one of more than a dozen companies involved in the Parkdale-led collaboration to produce the needed PPEs.
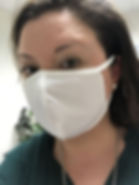
These face masks were knitted this week by Contempora Fabrics in Lumberton, N.C. Contempora is one of more than a dozen companies involved in the Parkdale-led collaboration to produce the needed PPEs.