
Posted November 27, 2017
OBERTSHAUSEN, Germany – Textile machinery provider KARL MAYER announced a series of equipment developments.
Revolutionizing the terry business
KARL MAYER develops and manufactures high-performance warp preparation machines for both weaving and warp knitting and, in order to do this, uses the synergies that exist between the two sectors.
The WKD-SP is the latest result of this know-how and technology transfer. This direct warping machine is based on the WARPDIRECT® machine for the weaving sector, and processes staple-fiber yarns.
Producers of warp-knitted, cotton terry towels should find this particularly interesting. This new machine delivers all the performance features of its predecessor but, above all, its advantages can be exploited by using back beams, with their wider widths, as sectional warp beams (SWBs) in the warp-knitting sector.
Die WARPDIRECT® is a universal direct warping machine for processing every type of staple-fiber yarn. It produces high-quality beams for the slasher dyeing process in denim dyeing, for combining all the yarns on the warp beams on the assembling machine, and for processing in a sizing machine with subsequent warp beam production. The back beams for these various processes are of the highest quality.
A terry warp-knitting machine writing headlines
KARL MAYER’s terry business continues to be a focus of innovation. Following the revamp of the TM 4 TS terry warp-knitting machine for processing staple-fiber yarns and its technical upgrade, together with various new textile developments, this company is now launching a new machine, which can produce an even greater range of patterns.
The designation of the new TMJ 4/1-T alone shows that it is something quite unique. This terry warp-knitting machine for processing filament yarns is the first of its kind with a jacquard bar included in the set of knitting elements, so that even lettering can be worked into towels, bathrobes and facecloths.
The jacquard bar on the TMJ 4/1-T enables new designs to be produced that have not been possible until now. Logos, lettering and floral effects can be worked, as well as geometric patterns and sweeping, decorative effects. Despite their fluffy surface structure, the pattern elements are extremely clear. They are worked and placed much more easily and flexibly than on the standard machine on one side of the fabric.
The fabric makes a sofa
Since the emergence of the athleisure trend, it has become clear that various synergies existing between specific segments of the textile sector can be exploited. For example, lingerie lace is being incorporated into the shirts of women runners, and functional materials are being used in sexy briefs. Home and household textiles can also profit from the transfer of ideas from one sector to another. For example, the possibilities offered by typical warp knitting machines used in the clothing sector are now bringing a touch of flamboyance to the home.
KARL MAYER has taken up this trend of transferring ideas from one sector to another in the textile industry and has used its tried-and-tested RASCHELTRONIC® machine to produce stable upholstery fabrics. This high-speed jacquard raschel machine has been a firm favorite among producers of sportswear and lingerie fabrics for some time now.
These companies are using the RASCHELTRONIC® to produce stretch and non-stretch textiles with functional zones. The model used is designated the RSJC 5/1 EL, and this new collection has made it an interesting proposition for manufacturers of home textiles as well. The fabrics feature an attractive, graphic design with open-work constructions, and are extremely heavy for RASCHELTRONIC® fabrics.
The final fabrics weigh between 330 and 400 g/m², depending on the arrangement of the weft lapping. In some designs, the weft runs along the holes, which therefore remain open, and does not join any stitch wales. In other patterns, the ground bars with the weft add to the openings, which affects the appearance and characteristics of the textile.
Securely packaged
KARL MAYER has revamped its machine technology for producing packaging sacks. As before, this fully integrated system enables ready-to-use, high-quality products to be manufactured non-stop from film at maximum efficiency.
What is new, however, is the machine’s level of flexibility. As the most important element, the double-bar raschel machine has been equipped with an EL pattern drive, which enables variable sack lengths and lappings to be worked.
An FTL unit is located at the beginning of the processing chain for producing sacks. This element in the production line has a cutting bar for cutting a double-layered, primary polyolefin film into tape yams and drawing them in a heating zone to produce monoaxial flat film yarns.
These yarns are delivered to the double-bar raschel machine, depending on the demand. The needs-based delivery of the tape yarns is a decisive factor for online process control, just as is the exact harmonization of the machine technology as a whole.
“With this non-stop sequence, everything must function perfectly and all the components have to be in perfect harmony, rather like an orchestra,” said Rainer Baier, a product developer, at the machine presentation.
Source: KARL MAYER
KARL MAYER announces series of new machinery developments
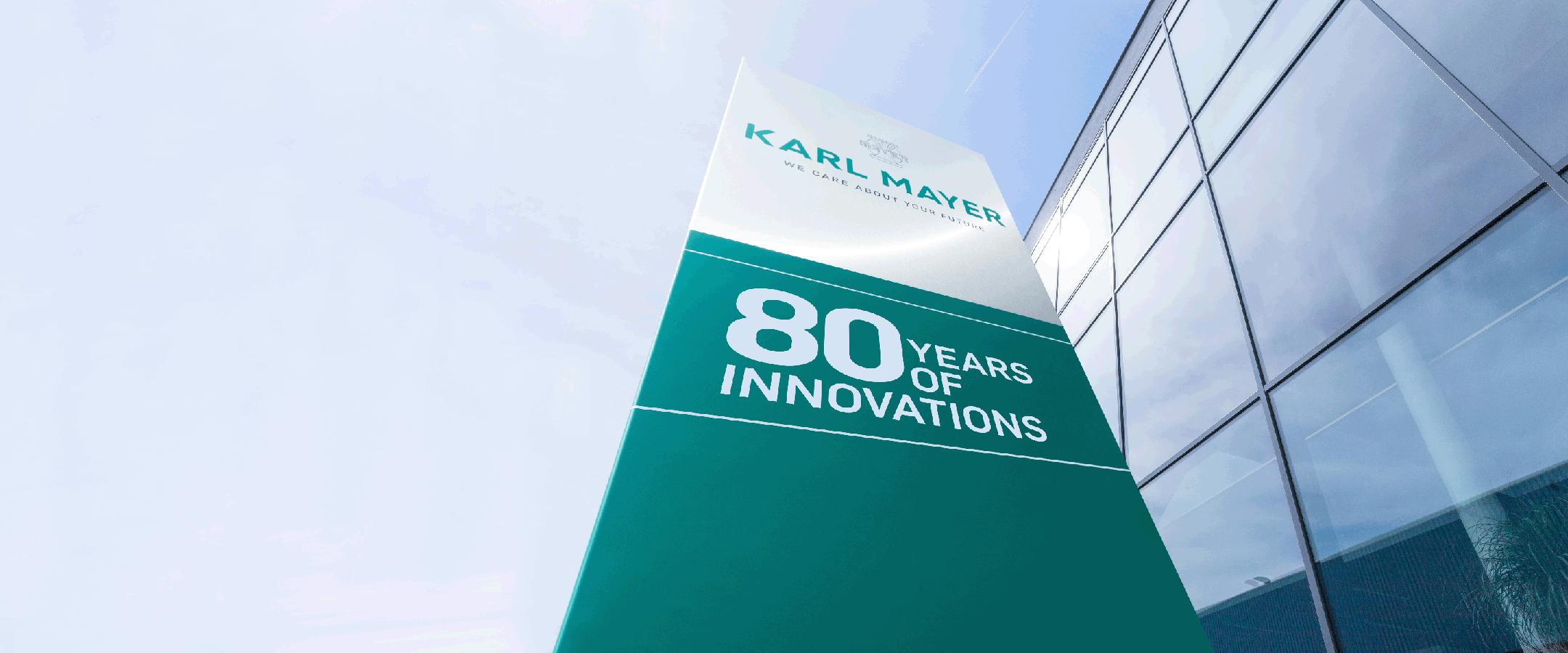