
Bob Pastene, executive vice president of Sales and Marketing for DRIFIRE, and Rob Hines, the company’s vice president of Product Development, gave an overview of the DRIFIRE® brand of flame resistant fabrics and flame resistant work wear.
Owned by Optimer Brands, DRIFIRE is a relatively young, small company with about 30 employees, but its products make a difference on the battlefield and behind the wheel of motorsports cars, they said. At the request of the military, the company in its early days developed an FR performance fabric that would not melt, Pastene said.
The high-performance FR features drirelease®, a patented fabric technology that enables brands to create performance apparel, the added. And all of its products are made in the U.S., they said.
DRIFIRE’s novel yarns yield fabrics capable of quickly absorbing perspiration from a wearer's skin and yet capable of quickly releasing that moisture, resulting in surprising levels of wearer comfort and wearer preference, Pastene and Hines said. They showed several videos highlighting the product.
A drirelease® customer who was looking for a new motorsports base layer that was SFI certified, featured soft compression was comfortable and had performance attributes approached DRIFIRE. The company subsequently designed four essential base layer garments and now has the only FR soft compression fabric on the market, Hines said.
Stretch, or compression, fabrics are the next evolution of FR base layers, he added.
DRIFIRE: From the battlefield to the track

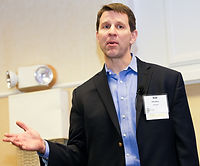
Rob Hines
Bob Pastene
Bob Pastene

Scott Margolin, International Technical director for Westex by Milliken’s Specialty Fabrics Division, introduced himself as the “guy who gets paid to blow stuff up,” before explaining why and how the company develops flame-resistant products. He showed a number of videos featuring various tests conducted to determine flame-resistance of fabrics under development.
“The most severe burns and fatalities are caused by non-flame resistant clothing igniting and continuing to burn,” he said.
He also showed some clips of actual arc flash fires with people wearing FR clothing and some who were not. He later showed a headline of a man who burned to death in an industrial accident.
“If that guy was wearing this stuff, he goes home to his wife and kids,” Margolin said. “That’s why we do what we do. It’s real and it happens almost daily. And it has to stop.”
Westex by Milliken mission: To save lives
Hardy Poole, vice president of Regulatory and Technical Affairs at the National Council of Textile Organizations (NCTO), provided an update on the Department of Defense-led Revolutionary Fibers & Textiles Manufacturing Innovation Institute (RFT-MII). DoD’s ManTech (Manufacturing Technology) office oversees the IMI process.
In March, President Obama announced a notice of intent (NOI) by the federal government to seek competition for creation of the RFT-MII. To start this process, the government was to enter a five-year cooperative agreement and provide federal funding up to $75 million to be matched or exceeded by funding from private industry and non-federal sources. After five years the RFT-MII is envisioned to become self-sustaining and be able to continue to add value to the domestic RFT area in perpetuity, according to ManTech.
Poole provided a timeline of events around the IMI selection process, which has now been narrowed down to three proposer groups, he said. He said the ManTech office has “gone black” in recent weeks and won’t release much information about where it stands in the process. He said the selection and announcement of the institute is expected before the end of the year.
Update provided on Fibers/Textiles Institute selection process
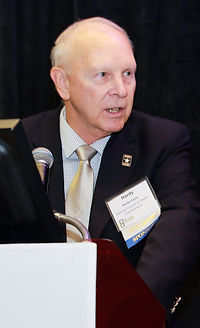
Under the title, “Go Where You Don’t Belong,” Kyle Blakely, director of Materials Development at Under Armour, discussed how and why the athletic apparel brand company goes about innovating.
“Our CEO talks about the zig and the zag,” he said. “When we see companies zigging, we try to zag. With that in mind, we started in apparel vs. footwear.”
Under Armour innovates in a variety of ways, Blakely added, including through materials development, and partnerships – as well as taking risks. “If it doesn’t feel risky, it may not be worth doing. That drives us.”
Under Armour innovation strategy: 'Zig when others zag'
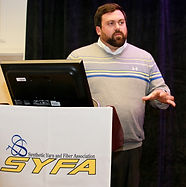
Innovating with partners is a shared investment that makes improves its capabilities, he added. “Under Armour doesn’t have the budget that some other companies have,” he said, “so we have to share our technology developments with our partners.”
The company wants to take its technologies and expand them into many different uses, he said. As such, it lets performance dictate the aesthetics of its gear, he said. It all comes down to “hitting the sweet spot,” he added, meaning developing a high-value garment that sells well at the right price point.
“We have not yet made our defining product,” said Blakely, an N.C. State College of Textile grad.

Nicholas Pence, vice president of Sales and Business Development at Coville, Inc., discussed “U.S. Cut and Sew: Trends in Military and Commercial Markets.” Coville manufactures knit fabrics and sewn products serving the private label and contract, military, personal protection and other market segments.
Pence, a decorated veteran, went over various facts related to military spending, industrial employment and retail spending, and how each affects the company’s strategy. And a big message was “U.S. cut and sew is still here,” he said, with California and Texas followed by the Southeast leading the way in garment production and four Southern states plus Maine employing the most knitting and weaving personnel.
Cut-and-sew challenges, Pence said, include the veritable skills gap, employee retention, aging and hard-to-find equipment, global wages and managing to run business consistently as it relates to volume.
He also discussed a number of action steps the industry can take to overcome these challenges. One step Colville has taken in the way of process improvements is through “team modules,” he said. “We put in some stand-up modules to try to work a little differently,” he said. “We have four to five sewers on an operation. We’re changing up how we do things, and we can be more diverse this way.”
In tackling these challenges, the textile and apparel supply chain is small enough in the U.S. that it needs to help each other through development projects and the like, Pence said.
Coville VP: U.S. cut and sew is still here

Dr. Jaime Grunlan, a Linda & Ralph Schmidt ’68 Professor in the Department of Mechanical Engineering, Materials Science, Engineering and Chemistry at Texas A&M University, offered a technical discussion on water-based, flame-retardant nanocoatings for textile blends from environmentally friendly, benign ingredients.
He showed flame-test results of tests on various intumescent flame retardants. He also illustrated how a layer-by-layer coating technique was used to deposit a highly effective flame retardant (melamine polyphosphate) from water onto polyester-cotton fabric.
Flame-retardant
nanocoatings
Rich Lippert, director of Business Development, Protective Market at Glen Raven Technical Fabrics (GRTF), LLC, gave an overview of innovation in technical textiles at the company. Using its core products as a base, the company has diversified into other markets and has grown and thrived as a result, he said.
Those segments include geosynthetics, military, automotive, filtration and protective. Lippert discussed products and how they were developed for each application.
The innovation behind Glen Raven Technical Fabrics
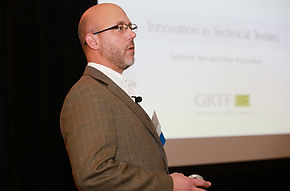
Filtration is the newest venture on which GRTF has embarked on, Lippert said. Seventy percent of the earth’s surface is water, but less than 1 percent is drinkable, he said. GRTF recognized this demand and designed fabrics used as permeate carriers in filter systems, he said. The company manufactures extremely thin fabrics, which allows the filter to be more energy-efficient with increased throughput.
“Our presence in most of these businesses was borne out of innovation,” he said. “And we innovate by cross-pollinating with our colleagues.”
Alasdair Carmichael, president of PCI Fibres (Americas), gave his latest update on raw materials, oil and fibers and added an update on large trade agreements.
““It’s actually been a fairly stable period we’re going through on the polyester raw materials side,” he said.
Oil prices are forecast to stay below $50, but beware of a surprise that may push them up to $60 a barrel, he said. Polyester raw materials are likely to follow oil, he added, noting that “maybe Chinese raw material producers will agree to a round of production cutbacks to tighten up the market.”
Carmichael also provided a closer look at the recently concluded Trans-Pacific Partnership (TPP) and the pending Transatlantic Trade and Investment Partnership (TTIP). Details of the former should be revealed in the coming days, but it will take time for the legislation to pass the U.S. Congress, he said.
In addition, he discussed recent antidumping claims by the five largest import suppliers of PET resins, which preliminarily appear to have been successful.
Update given on raw materials, trade, antidumping claims

In his economic overview, Dr. Roger Tutterow, professor of economics and director of the Econometric Center at the Michael J. Coles College of Business at Kennesaw State University, said U.S. manufacturing has made a good comeback, but it’s now moving sideways due to the value of the dollar.
Earlier this year, as the U.S. dollar rallied against trading partners, it has hurt the U.S. on its trade numbers, he added. But rising labor costs in Asia is contributing to the reshoring effort here, he said.
On the overall economy, he asked, as we finish the sixth year of the recovery, has “normal” finally arrived? “This has been a timid recovery,” he said.
He went on to cover most of the leading economic indicators, including oil prices, consumer sentiment, employment, shipments and construction spending. “Finally today, both residential and non-residential construction is up for the first time during the recovery,” Tutterow said, “and home prices are rising again, which is good news.”
Has 'normal' finally arrived in economic recovery?

Posted November 2, 2015
By Devin Steele (DSteele@eTextileCommunications.com)
CHARLOTTE, N.C. – About 150 industry professionals attended the Fall Conference of the Synthetic Yarn and Fiber Association (SYFA) here last week. And that’s the biggest turnout this group has seen for a semi-annual gathering in recent years, according to association President Roger Crossfield of CTW Development Company, LLC.
Nine speakers provided presentations in their areas of expertise, many of them around the conference’s theme, “Hot Textile Technologies: Function for the Extreme,” particularly related to flame-retardant (FR) textiles.
Below are highlights of those speakers’ discussions.
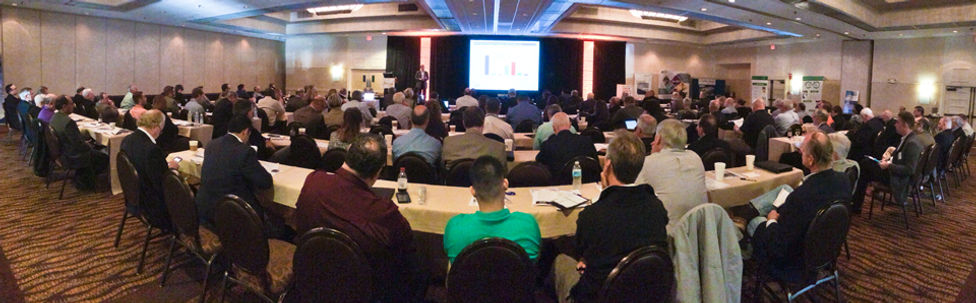
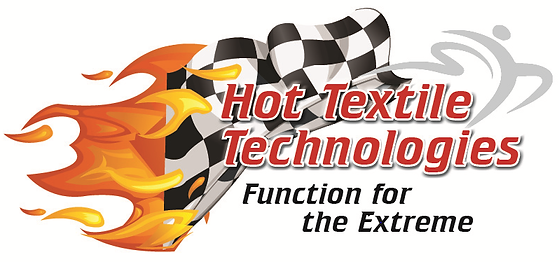
SYFA conference attendees find out what's hot

SYFA President Roger Crossfield of CTW

Meredith Boyd of Unifi, Inc. introduces speaker.

Mike Becker Jr. of Michael S. Becker, Inc. introduces speaker.

SYFA President Roger Crossfield of CTW