
Attendees from 27 states and three foreign countries learned the latest trends and collected information aimed at improving quality and production efficiency while reducing lead times, according to moderator Mike Fralix, president of [TC]2, Cary, N.C.
No less than 13 presenters filled the day with information about such topics as product development, labor costing, automation, connectivity, technology implementation, tracking, products and raw materials.
“You are all in for an outstanding lineup of presenters who will arm you with information that you will take back to your manufacturing companies,” said SPESA Chairman Mel Berzack of Sewn Products Equipment Co., Jefferson, Ga., in introducing the program. “When making future decisions, these words will be very prominent in how you make those decisions. And I say this emphatically because this is our fourth such session and I’ve talked with participants who have been here in the past and, without exception, they’ve all taken bits of information from this seminar and used it for their success going forward.”
In his presentation to end the day, Frank Henderson, president of Alabama-based Henderson Sewing Machine Co., called these days the “The Age of Disruption” as the sewn products industry embraces the re-shoring movement, robotics and automation and other new technologies.
Trends in product development
Adam Smythe of Human Solutions of North America, Cary, N.C., kicked off the day by covering trends in product development as it relates to paradigm shifts in consumer goods and fashion. In particular, he spoke about 3D virtual and knowledge-based design and integrating the customer into product development.
Using integrated systems help make for a seamless process from concept to consumer, he said, adding that product fit data is inherent in the system and process. A key is fitting clothing to people instead of people to clothing, he pointed out.
Smythe also gave trends in global anthropometric (measurement of a human being) data, which enables producers to optimize fit and comfort for both ready-to-wear products and individualized products, he said. Access to digital anthropometric data is a source for product innovation and customer communication, he added.
Meanwhile, Ram Sareen, chairman, CEO and founder of Los Angeles-based Tukatech, which offers patternmaking, design and manufacturing software, spoke of the challenges of product development. Some of those challenges arise from the fact that cloth-to-cloth on form garments drape differently, and body shapes and testing fit methods are not exactly the same.
Posted Septebmer 22, 2015
By Devin Steele (DSteele@eTextileCommunications.com)
CHARLOTTE, N.C. – Nearly 100 members of the apparel and sewn products industry and its supply chain attended the Advancements in Manufacturing Technology Conference, hosted by the Sewn Products Equipment & Suppliers of the Americas (SPESA) here last week.
‘The Age of Disruption’
Sewn products reps get peek at new technologies
![]() |
---|
![]() |
![]() |
![]() |
![]() |
![]() |
![]() |
![]() |
![]() |
![]() |
![]() |
![]() |
![]() |
![]() |
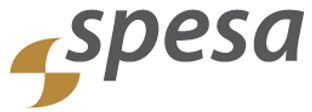

“Look at what needs to be done, figure out how to do it and how to make it here. Made in the USA – that should be our focus. Let’s make it happen. Let’s not say ‘just get the monkey off my back and let somebody else handle it.’ Do it yourself.”
Ram Sareen
Chairman, CEO & founder,
Tukatech
To tackle these issues, Tukatech has developed 3D motion analysis software that simulates garments on a body in motion. In a static pose, a garment on a 3D model may look like it fits, but this tool offers real-time animation that analyzes the true fit behavior at each frame of movement – including squatting, he said.
In his closing remarks, Sareen provided good food for thought not only for attendees but for the entire U.S. apparel and textile industry: “Look at what needs to be done, figure out how to do it and how to make it here,” he said. “Made in the USA – that should be our focus. Let’s make it happen. Let’s not say ‘just get the monkey off my back and let somebody else handle it.’ Do it yourself.”
Upfront labor costing
John Stern, president & CEO of Methods Workshop, West Palm Beach, Fla., provided a detailed look at how upfront labor costing can improve your bottom line. He offered a brief history of the Methods-Time Measurement (MTM), a predetermined motion time system that is used primarily in industrial settings to analyze the methods used to perform any manual operation or task, and as a product of that analysis, set the standard time in which a person should complete that task.
Today’s version of that system, PMTS (Predetermined Motion Time Sensors), is the only way to meet the requirements for the “right product” at the “right time” at the “right time,” he said. PMTS is frequently referred to as Standard Time Systems, he added. As an example of PMTS, he showed charts related to data acquired for setting a shirt pocket, concluding that the total time to perform this task with allowances is .85 minutes.
Stern went on to note that, finally, a Standard Data System for non-engineers is available, which he called “upfront costing.” That system helps the merchandiser, the manufacturer and the sourcing group enhance their speed to market, he said. The system is accurate, consistent and fast, he pointed out, adding that it can be used at the designer level at the same time the garment is being created.
Spreading/cutting room management
Michael Rabin, country manager for Morgan Tecnica America, Montreal, discussed spreading/cutting room management. “I am glad to see manufacturing moving back to America, but with that comes challenges,” he said in his opening remarks.
In today’s highly competitive market, manufacturers are faced with a completely new set of challenges, he said. To be successful in a global market, they need to be prepared to reduce quantities, provide more complexity in styles and fabrics, reduce lead time, be cost competitive and increase quality standards, he added. And without a proper workflow and automated systems to support, the success rate is low, he noted.
He went on to share some solutions that can be applied to any cutting room today, he said, centered around optimization, management, automation and analytics.
To automate … or not to automate?
In his best Hamlet impersonation, Berzack asked that question, before providing several examples of how automation is helping the sewn products industry.
After showing those videos of automation at work, he said, “the answer to that question is ‘absolutely, definitely.’ ”
Later, Henderson gave an interesting presentation on robotics and automation. He prefaced his remarks by pointing out that apparel manufacturing in the U.S. has declined by more than 80 percent over the past two decades.
But a number of factors have played a large role in the re-shoring movement back to the U.S., he said. Among them: rising labor and energy costs in China, increasing transportation costs and longer order lead times. And greater speed to market is a top priority in global sourcing, he added. Henderson also noted that more than 97 percent of apparel sold in the U.S. is being manufacturing globally – and not near this market.
Henderson said that these issues are pushing sewn products manufacturing back to this hemisphere and closer to the largest consumer market in the world. And repetitive motion jobs are jobs that can be automated today. He provided a number of examples of robotic technologies that are now more affordable and flexible.
In the future, we should expect more factory automation, 3D sewing, autonomous work cells and vision systems integration, he concluded.
Connectivity in the cutting room
Ron Ellis, product director at Gerber Technology Systems Group, presented “Integrating Technologies to Move from Inspiration to Market.” Technology can and is driving innovation that can help you companies deal with product design and development, supply chain management and managing how and where products are taken to market.
But, according to a recent Gerber study, common challenges exist among the value chain in bringing products to market, including: competitive market pressures drive the need for speed in product development cycles; costing operating pressures require an efficient and agile supply chain; and technology convergence creates the need and desire for all data to be connected from step to step in the process.
His presentation covered numerous new technologies that have provided better connectivity in the fashion industry. For one, the “Internet of Things” provides a seamless connection between design, development, sourcing and the manufacturing floor, he said.
Keys to successful new technology introduction
Brandon Sexton, vice president of Professional Services for Lectra North America, discussed change management, particularly as it relates to new technology projects. Throughout his presentation, he used Dilbert cartoons to illustrate pain points associated with change, in a humorous fashion.
The most critical factor impacting the success of any transformation is leadership’s ability to define and leverage its vision for change, said. This vision should serve as the basis for every decision made and every action taken from the inception of the project through the sustaining activities long after the project has ended.
Technologies and products
Rick Frye, director of sales and marketing at Brother International Industrial Products, offered updates on advancements in single-needle lockstitch and electronic programmable sewing machine technologies.
Of particular note, he showed through video, is a system has been developed that is integrated with a programmable sewing machine an employs an industrial PC with software, a custom camera and lighting, to “automatically” create a stitch pattern around the perimeter of a regular or irregular shaped object (patch, label, applique, etc.) within the sewing area of the machine.
Jose Reyes, technical manager at Schmetz Needle Corp., provided a look at innovations in cutting needles and how to select the right one for a particular need, pointing out that 3,500 types of needles are available.
Phillip Freese, technical director, Global Retail Solutions for American & Efird, Mt. Holly, N.C., presented a mini-workshop dubbed “Threaducation.” He discussed how proper thread selection can contribute to increased productivity, lower manufacturing costs, higher quality products and improved profitability.
Using a higher quality thread, he said, will reduce sewing interruptions and thread breaks, reduce repairs, lower overhead, reduce payback time on equipment and reduce production lead times, among other benefits.
Patrick Weissgerber, president & CEO of Dap Americas, Norcross, Ga., gave a review of different welding technologies, their possibilities and limitations in the manufacture of sewn products.
Real-time visibility
Joey Knight of Cherry Shop Floor Controls, Atlanta, discussed how real-time information enables manufacturers to increase speed to market, improve efficiency and enhance quality while reducing overall production costs. To effectively manage, manufacturers require immediate and relevant data about what is happening on the plant floor, he said.
Leveraging real-time technology, he said, increases supply chain visibility; improves operator, group and team productivity; balances production flow; reduces on-and-off standard costs; provides better statistical quality control; and offers a machinery history and parts control.