
Posted September 14, 2016
By Devin Steele
CHARLOTTE, N.C. – About 55 participants from 46 institutions representing the value chain from universities, industry and government gathered here last month to get the latest scoop on soy technologies and research projects related to fibers and thermoplastics.
During the annual Fibers and Thermoplastics Technical Advisory Panel (TAP) meeting, attendees were updated on developments to bring soy derivatives to market.
COOL BEANS
Researchers present latest scoop on soy uses in fibers, thermoplastics
![]() |
---|
![]() |
![]() |
![]() |
![]() |
![]() |
![]() |
![]() |
![]() |
![]() |
![]() |
![]() |
![]() |
![]() |
![]() |
![]() |
![]() |
![]() |
![]() |
![]() |
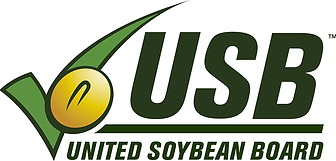
The meeting was coordinated by Omni Tech for the United Soybean Board (USB), which also sponsors TAPs for thermosets and rubber, as well as adhesives, coatings, papers, solvents and inks. During the two half-day sessions, speakers provided project updates on soybean derivatives developed through its sponsored research and were able to get input from industry representatives.
“I thought the TAP meeting went very well,” said Robina Hogan, Charlotte-based commercialization manager for fibers at OmniTech. “This has been a great avenue for these projects to generate industrial interest and share technical information between researchers. It showed significant progress in research activities, some of which are moving into pilot and commercial evaluation levels. Audience participation was excellent. This was the first fibers’ TAP meeting that a USB director was in attendance. He asked many questions, which showed attendees that the program is of great interest to soy farmers.”
That board member would be Robert White Jr., a soybean farmer based in Virginia Beach, Va., who said he was “very impressed” with the project overviews he heard.
“It continues to amaze me how many different things that can be made from soy flour, soy oil, soy protein and soy meal,” he said. “And many of these projects are being conducted with the new sustainability protocol of the USB, and a lot of these green technologies can be done cheaper than standard technologies.”
The first Fibers and Thermoplastic TAP meeting took place in 2009 when USB started funding in those areas. Many of the projects have been ongoing and are moving closer to commercialization, Hogan reiterated.
“I do see some of these technologies coming to market,” she said. “There are several that have corporate sponsorship now. There are, however, hurdles to overcome. We have finally understood what is needed to viably make an economical feasible compounded resin and now we need to understand the scale-up and commercial opportunities in fibers, films and other thermoplastics.”
Hogan, who has been involved in this TAP meeting since its inception, added that she continues to be impressed with the emerging uses of soy products.
“We have found that we can blend soy into PE (polyethylene), PP (polypropylene) and PLA (polylactic acid) so far and enhance biodegradability, change the fiber feel and make hydrophobic materials hydrophilic,” she said. “We have found soy can be used to make new textile sizes with performance comparable to PVA (polyvinyl alcohol) sizes. We also have found uses for soy oil in making monomors/polymers, surfactants, coatings and plasticizers, to name a few.”
Hogan, in kicking off the program, noted this general summary of fiber related to the soy projects:
-
Initial soy copolymer blend development with PE, PP, POE, PVA and PLA are in pilot stage scale-up for fibers and nonwovens;
-
Soy/cellulose/chitisan film process work is now looking for commercial opportunities;
-
Soy hull-based cellulose pulping technology was developed, and several commercial discussions are ongoing – bi-component fibers using soy hull pulped micro fibrils (ribered) have been developed with PE and PP for geotextiles;
-
Solution blowing technology with SP-nylon, SP-POE and SP-PAN was demonstrated and six-position scale-up was achieved at Biax. Commercial pilot equipment design is being defined;
-
U.S. Army Natick has developed blends for films with PE, PP, PLA and for films;
-
Aktiv has developed melt-extrusion technology for ultra-high-molecular-weight polyethylene (UHMWPE) and soy chemistry for ropes;
-
Technical activity with NatureWorks for fiber opportunity is underway;
-
Elastomeric polymers are being developed;
-
University of Nebraska cellulose stalk fiber and University of Illinois paper have been researched and scale-up development is being developed;
-
Commercial soy fiber technology is used by a nonwovens company; and
-
Commercial activities are underway with the use of soy sizing.
Highlights
Mike Erker, bioproducts development director at SmithBucklin & Associates, St. Louis, provided an overview of the United Soybean Board, noting that it is governed by 70 board members and represents more than 600,000 soybean producers. USB’s industrial objective, he said, is for soybean oil or meal to be viewed as a viable alternative to traditional petrochemicals because of soy’s performance, costs and sustainability story.
Dr. JoAnn Ratto, research engineer for the U.S. Army Natick Soldier Systems Center, Natick, Mass., presented an update on work her group is doing to create flexible, multilayer military packaging from soy meal and waste stream-based blends, and highlighted other applications being researched.
Abhay Joijode of The Nonwovens Institute at N.C. State, Raleigh, N.C., covered a project his group has undertaken to test the blending and coating of cotton yarn with soy products, PLA and bio-PE, as well as coating cotton yarns with polymer/soy blends to obtain fully bio-based component fibers.
Dr. Chuanbing Tang of the University of South Carolina, Columbia, S.C., brought three members of her group’s “soybean team” and discussed their research, which involves the use of monomers and polymers to produce thermoplastics and elastomers. So far, she reported, they have discovered: a new synthetic method to scalable soybean oil monomers and polymers preparation; bio-plastics with high strength and thermo-stability from nanocomposites with CNCs; elastomers from soybean oil polymers with high-elastic recovery; and epoxy resins from soybean oil polymers.
Dr. Amod Ogale, director of the Center for Advanced Engineered Fibers & Films (CAEFF) and Dow Chemical Professor, Chemical Engineering at Clemson University, Clemson, S.C., highlighted a project to modify soy oil precursors suitable for conversion into carbon fibers – which have large market potential if produced from bio-based, sustainable and greener means, he said. Ogale also covered another project in which his team is involved that’s aimed at developing a continuous, melt process for converting soy-based flour into non-food, value-added products such as fibers and nonwovens.
Roger Crossfield of CWT Technologies, LLC, Charlotte, N.C., went over a project designed to identify and commercialize soy materials that provide significant enhancements in the performance properties of polylactic acid (PLA). He noted that PLA is finding a home in a number of fiber, film and molding applications, adding that the commercially viable, technically advantageous combination of soy materials with PLA would be a significant advance in bio-renewable polymer technology.

Dr. David Grewell, professor in Agriculture and Biosystems Engineering at Iowa State University, Ames, Iowa, gave an interesting summary of work being done on soy-based lawn, field and horticultural products.
Dr. Dharma Kodali, research professor in the Department of Bioproducts and Biosystems Engineering at University of Minnesota, Minneapolis, discussed development work of high-performance bio-plasticizers from high oleic soybean oil.
Keith Masavage of BioBent Polymers, Columbus, Ohio, discussed a project aimed at accelerating commercial adoption and volume production soy-based thermoplastics. The objective is to convert, mold and test four of Commercial Vehicle Group’s (CVG’s) highest-volume resins. CVG is interested in assisting BioBent achieve full-scale bio-plastic production, he said.
Tom Fields of AkTiv, Inc., Medina, Ohio, and also a soybean farmer, offered an update on a second-generation MoorGuard Fiber being developed from soy products for marine and other applications. The product is nearing commercialization, he said.
Dr. Jinwen Zhang, professor in the School of Mechanical and Materials Engineering, Washington State University, Pullman, Wash., talked about how soy protein, combined with polyacrylic acid, can be a super absorbent polymer and has a lot of potential applications.
Dr. Yiqi Yang, Charles Bessey Professor in Textiles, Merchandising & Fashion Design and Biological Systems Engineering at the University of Nebraska, Lincoln, Neb., noted that, currently, nothing can replace PVA in textile processing, but his team is evaluating dispersants from functionalized soybean oil as an alternative in sizing. He concluded that soymeal could potentially substitute PVA sizing, but research continues. “The market interest in this project is phenomenal,” Hogan said after Yang’s presentation.
Dr. Thomas Theyson of TensTech, Inc., Matthews, N.C., highlighted a project related to soy oil-based polymeric surfactants. He noted that the technology offers attractive economics, high biodegradability and the potential for high annually renewable bio-content. TensTech is now working with the Nalco/Champion division of Ecolab that is capable of carrying this technology forward, he said.
Dr. Carlos Salas, professor in the Department of Forest Biomaterials at N.C. State University, Raleigh, N.C., presented a project his team is working on to introduce a surface finish treatment based on soy protein, which can be applied to different hydrophobic fibers and nonwovens from different polymers; and to develop both surface finishes and antibacterial technologies based on a combination of soy protein with appropriate components.
Jeff Cafmeyer, polymer scientist at Battelle Memorial Institute, Columbus, Ohio, and Rob Roden, director of Innovative Manufacturing at Steer America, Uniontown, Ohio, discussed a project they’re collaborating on with the USB to replace a significant portion of acrylic acid in hydrogels with inexpensive soy flour while maintaining water uptake values. Hydrogel is used in many applications, from health care to agriculture, and most are petroleum-based, they said. But adding renewable content to the polymer increases the renewable carbon footprint and enables biodegradation of the hydrogel, they added.