
Collaborative, entrepreneurial spirit shines at Shima Seiki’s Global 3D Knitting Seminar
Posted June 8, 2017
By Devin Steele (DSteele@eTextileCommunications.com)
BROOKLYN, N.Y. – Building on the success of two similar events in Los Angeles, Shima Seiki U.S.A., Inc. organized its third Global 3D (G3D) Knitting Seminar & Workshop here recently, attracting nearly 200 knitters, fiber producers, retailers/brands, associations, academia, entrepreneurs and others.
Appropriately, the two-day event was hosted by the Brooklyn Fashion + Design Accelerator (BF+DA), a collaborative space for ethical fashion that provides designers with resources to transform ideas into successful businesses. The 21,000-square-foot BF+DA, spearheaded by the Pratt Institute, has a “micro-run” production facility with computerized knitting, a shared cut-and-sew space, a sustainability lab and digital printing for textiles.
“The BF+DA is a vibrant community of designers and entrepreneurs dedicated to ethical, sustainable and innovative products,” said Deb Johnson, the accelerator’s executive director.
The purpose of the symposium was to bring together representatives from across the textile and apparel supply chain to collaborate, educate and focus on the future of the industry, according to Seiichi “Senna” Nakaya, president of Shima Seiki USA, the U.S. subsidiary of leading Japanese flat knitting machine manufacturer Shima Seiki Mfg. Attendees heard several success stories of companies, universities and other entities that are using Shima Seiki technology.
In addition to Shima Seiki machines already at the BF+DA, the company had on display for demonstration its flagship MACH2XS WHOLEGARMENT® knitting machine featuring the original SlideNeedle™ on four needle beds and spring-type moveable sinkers. Representatives also demonstrated its APEX3 design system, which provides comprehensive support throughout the apparel supply chain, integrating production into one workflow, from yarn development, product planning and design to production and even sales promotion.
Bringing 3D knitting to scale
Among 20 speakers was Pano Anthos, managing director of XRC Labs, who presented a straight-talk discussion on how to enable 3D knitting to go mainstream. He is deeply enmeshed in this topic, working for a company that serves as an accelerator and fund for the next generation of disruptors in the retail and consumer goods sectors, he said.
XRC’s vision, he said, is “to be at the forefront of change, disrupting the conventional system of retail, promoting the best experience for consumers and producers, and creating an ecosystem that matches partners for success.” XRC represents more than 300 start-ups in six countries, he said.
Bringing 3D knitting to scale requires companies to increase their speed by three or four times, produce a niche product and enable the user to personalize the product, Anthos said.
“Uniqueness raises margins,” he said. “And a willingness to pay is the amount of money a person is willing to pay to get or avoid something other than the status quo.”
He explained the difference between mass customization and personalization, noting that pre-defined attributes in a product is customization. “Personalization is different – and it’s powerful,” he said. “It enables the user to personalize a product to their liking, and one in five customers say they are willing to pay a 20 percent premium for personalized products.”
And personalization requires APIs, which basically allows users to build on top of technology, he added.
“Zynga became a billion dollar company on the back of an API, and an API created Facebook,” Anthos said. “It behooved Apple to have an API in place because Apple knew it was not good at building apps.”
He closed by encouraging Shima Seiki to enable APIs, which would allow users to take personalization to another level, he said.
“Shima Seiki is not Superman, so I would suggest it create a way for people to talk to the machines,” he said. “Customers want this – they’re personalizing all kinds of things. They designer should have an API.”
Taking off like Wildfire
Mike Moody, Vanguard Pai Lung’s vice president of Product Development, gave an overview of Vanguard Pai Lung’s Wildfire Division, a radically new initiative aimed at bringing knowledge and technology back to the Western Hemisphere. Specifically, the goal is to help brands, designers and manufacturers, through education and technical expertise, develop innovative fabric technologies that transform end results, he said.
Moody, the self-described “machine guy,” is on a whirlwind mission around the country with his partner Mandi Strickland, “the textile techie,” to spread the word about Wildfire, he said. The initiative aims to improve cycle time, reduce development costs and enable more efficient mill sourcing.
“This also enables you to own your own fabric IP,” said Moody, whose Monroe, N.C.-based circular knitting machine manufacturing company traces its roots back to 1916 in Brooklyn.
Customers include “industry disruptors” who want to deliver unique product to their customer “now,” he said. These include entrepreneurs, manufacturers and brands.
Wildfire uses Shima Seiki’s APEX3 to create digital knit specs, which is only language needed for users to commnicate knits with the rest of the world, he said. The digital knit spec allows empowers customers to knit without a sample, he said.
Customers can knit at the company’s Innovation Lab, creating sample fabrics in real time, fast, he added. Collaborating with Wildfire’s expert staff and Innovation Lab in enables users to reduce layers in the process, discontinue the physical mailing of swatches and enables faster material approval times, he said.
“Pretty cool, but what else does Wildfire offer?” Moody asked, before explaining that the initiative offers 1) trend research, classified by machine type in meaningful colors, function, and surface interest; 2) fiber and yarn selection; 3) a material library for design inspiration developed by machine type in reproducible, vetted constructions; and 4) reverse engineering in order to replicate seasonal designs and identify knitting machines required for production.
Disrupting traditional manufacturing
Veronikia Harbick, who co-founded Thursday Finest with her husband Michael Carlson in 2015, discussed their Brooklyn-based start-up. Using a Shima Seiki machine, the company provides 3D knitted products such as neckties, socks, hats and scarves in custom color combinations and sizes.
By creating custom products in minutes, the company is changing the consumer retail experience and how products are made and sold, Harbick said. The concept is one of the disrupters of traditional apparel manufacturing, she added.
“We make custom apparel on demand in a matter of minutes,” she said. “We have a dialogue with our customers, which is important to our mission. It is product co-creation. In rethinking manufacturing, we can see this concept to light. Consider it omni-channel manufacturing.”
Among its products are personalized, foot-shaped socks contoured for each foot, and can include customized words on them.
Protecting against mosquitoes
Dr. Andre West, assistant professor at N.C. State’s College of Textiles, went over a project in which he is engaged aimed at developing comfortable, non-chemical garments to protect against mosquito bites, using novel textile design. With 725,000 people killed every year, mosquitoes are the world’s deadliest animals, so the need exists for such garments – and the market is enormous, he explained.
The problem is now is that current vector protective clothing does not meet the needs for at-risk civilians, he said. Working jointly with N.C. State’s College of Natural Resources and College of Agriculture and Life Sciences, the team has developed a non-chemical, bite-proof solution that is 99.9 percent effective, he said. The garments were developed for the market, with the first target being pregnant women susceptible to the Zika Virus, he said.
“The clothing is safe, containing no insecticides,” West said. “It also is economical, environmentally sustainable and comfortable for indoor and outdoor use in hot, humid climates.”
He went on to explain the technical of the fabric technology and how it works, adding that the initial focus is to create a line of sustainable, non-chemical, culturally appropriate, fashionable maternity clothes.
adidas initiatives
Saraa Green of Portland-based adidas presented on both days of the event. She first discussed a major project in which the well-known brand is engaged in partnership with Parley for the Oceans, an organization that works to end the destruction of marine life. The program is aimed at removing plastic pollution from oceans and transforming it into high-performance sportswear.
“We want to become a leader in sustainability and protect the oceans,” she said.
adidas works with partners such to collect, sort, clean ocean plastics and create apparel and footwear. The company recently released “Parley” versions of its most popular Boost running shoes in ocean-inspiring colors, she said.
On Day 2, Green explained a new shoe, FutureCraft 4D, that adidas has developed with a Silicon Valley-based company, Carbon, using Carbon’s pioneering digital light synthesis technology. “This is the world’s first high-performance footwear featuring midsoles crafted with light and oxygen,” she said.
The process uses digital light projection, oxygen-permeable optics and programmable liquid resins to generate durable products, she explained. By the end of 2018, adidas plans to produce more than 20,000 pairs of of shoes using this technology, she added.
“This shoe has direct benefits to the athlete, including precisely tuned functional zones in the midsoles,” Green said. “It addresses specific needs of cushion, stability and comfort.”
Tackling smart fabrics
Matt Kolmes, CEO of Hickory, N.C.-based Supreme Corp., presented, “Secrets of the Smart Fabric Toolbox,” explaining a project the company is working on to improve the conductivity of yarns and sewing threads.
The problem with yarns and sewing threads, he said, is they have limited conductivity and/or durability, and encounter processing issues such as an inability to cross seams, to be machine sewn and for the fibers to cross over themselves.
“We’re trying to bridge the gap between the language textile people speak and electronics people speak,” Kolmes said.
He explained trials that Supreme is conducting to address these issues, but due to the proprietary nature of these tests, results will not be shared here. But a new product around this research is expected to be launched at this year’s IFAI Expo in New Orleans in September, he added.
Yarn: The next ‘invention’
Michelle Letendre, who co-founded The Textile Foundry with Stephanie Rodgers, explained that its mission is to enable designers, developers and engineers to achieve more with textiles through development expertise. The entity, which supports U.S. manufacturing, also serves as an educational resource with a focus on the foundational stages of textile development (yarn and textile formation), she said.
She discussed the textile development process, which can be lengthy, and the roadblocks encountered along the way. They called this a “revolutionary time in textiles.”
Letendre surmised that yarn is the “next invention,” because it is the basis for textile development. “It’s the first step in the textile process and the foundation for something greater,” she said. “End use is critical to the development of the right textile the first time.”
She went on to talk about The Yarn Connexion within the Foundry, aimed at reducing or eliminating the lengthy yarn development process; getting brands and end users to product faster; reducing costs; elevating yarn performance; and putting a system in place to transition to scale-up.
As such, the Foundry is collecting a yarn library of various types (synthetic, natural and specialty) and is currently using a Shima Seiki SWG-041 15-gauge knitting machine for sampling, she said.
Other speakers
Other speakers included:
• Shari Litow of Honeywell, who discussed the company’s Spectra fiber, known as one of the world’s strongest and lightest manmade fibers, she said.
• Genevieve Dion, assistant professor in the Westphal College of Media Arts & Design and director of the Shima Seiki Haute Technology Lab at Drexel University, who explained the work the university is doing to develop functional smart fabrics in conjunction with Advanced Functional Fabrics of America (AFFOA);
• Carrie Yates of Cotton Incorporated, who talked about performance cotton knitwear, a collaboration with Shima Seiki USA, as well as a natural approach to cotton knitwear that requires no dyeing, minimal finishing and is more responsible;
• Allison Bowles, an N.C. State research assistant, who explained projects students are working on using Shima Seiki technology;
• Bethany Pollack of Propel LLC and Jim Owens of Nautilus Defense, companies that have partnered on a project related to a wearable advanced sensor platform;
• Will McHale, director of the Parsons School of Design, which recently installed two Shima Seiki machines and will be using them in its design curricula going forward;
• Kostika Spaho, 3D program lead at Fuerst Group Innovation Lab, owner of the KEEN footwear brand and a user of the Shima’s APEX3 system, who gave a virtual reality demonstration used for consumer simulations;
• Gihan Amarasiriwardena, co-founder of Boston-based Ministry of Supply, a high-performance business wear men's fashion brand launched in 2012 and also a Shima Seiki machine user;
• Liz Hilton, owner of Grand Rapids, Mich.-based KnitIt, a knit development specialist that uses the 3D knitting solution to create one product in one product for any industry or end use, including healthcare, office furniture, consumer electronics, automotive and wearable technology;
• Kevin McMullan of Toray International America, who discussed his company’s plant-based polyester, its applications and advantages in today’s sustainable environment;
• Masayuki Yumiyama of Shima Seiki, who presented an overview of WHOLEGARMENT customization; and
• Akira Tuno of Shima Seiki, who also demonstrated WHOLEGARMENT technology.
Posted June 8, 2017
BROOKLYN, N.Y. – This has been an “extraordinary” year for Shima Seiki USA, according to company Vice President Matt Llewellyn.
“The year started off with a big bang as we collaborated with Intel at the NRF show to promote improvements in the USA apparel supply chain using Intel technology,” he said.
At Intel’s during the NRF – called “Retail’s BIG Show” – Shima Seiki exhibited its M153XS WG WHOLEGARMENT knitting machine and its Apex3 design system.
“The event was a big success and created much interest in a new phrase I hadn’t heard before – ‘back-door production.’ ” he said.
“This concept means localized production with on-the-fly changes in style or color to capitalize on fast-changing trends, which drastically reduces inventory, shipping and travel expenses, yet improves factory communication and shorter supply chain,” Llewellyn said. “These benefits can easily outweigh the benefits of lower-cost Asian imports and fits mass customization, e-commerce and smaller fashion companies. This concept also fits into many sectors of our industry such as medical and industrial applications.”
Using this “back-door production” model, Shima Seiki USA targeted Brooklyn for the third edition of its Global 3D (G3D) Knitting Seminar & Workshop after two successful events of this kind in Los Angeles, said Seiichi “Senna” Nakaya, president of Shima Seiki USA. The New York fashion market is massive and covers the entire spectrum, from large retail to boutique to coterie and more, he added.
“We believed by introducing new innovations from fiber, machinery and products, the event would continue the momentum we felt at NRF, and it certainly did,” he said.
With nearly 200 attendees over the two days, it was Shima Seiki USA’s largest event of its kind yet, Nakaya said. On display at the workshop was Shima Seiki’s M153XS 15G WHOLEGARMENT machine.
“The reason for bringing this machine to the event was very clear,” Llewellyn said. “By eliminating much of the labor costs related to apparel manufacturing and at the same time making a garment that fits and feels better, new doors can be opened for American companies seeking fast production for off-shelf or customized garments. The ‘back-door production’ concept and the M153XS enables retailers to replenish their shelves as the items are sold and, immediately be able to capture a trend whether it be a style change or color change.”
The concept also helps domestic companies eliminate the need for ordering Asian product 18 months in advance without knowing how trends will change or having excess inventory due to market trends, Llewellyn added.
Also displayed in Brookyn was the Apex3 design system.
“The Apex has every tool a textile designer would ever need to help create new styles in woven, flat knit or circular fabric,” Nakaya said. “From simulated or scanned yarn to 3D-rendered avatars displaying your garment before being produced helps shorten the supply chain dramatically. It also gives designers the power to create styles with very specific details to factory such as color, yarn and machine data.”
The Apex3 is currently being used across many sectors of the industry, including retailers, fashion designers, major apparel brands, industrial component and medical component manufacturers.
“We were excited to see the American entrepreneurial spirit alive and well,” Llewellyn said. “The G3D3 proved there are many young, talented people coming into our industry and they’re thinking outside the traditional box. This is our future and I’m proud to say Shima Seiki is helping these talented people find an answer to their dreams.”
– Devin Steele
Brooklyn event augments Shima’s ‘extraordinary’ year
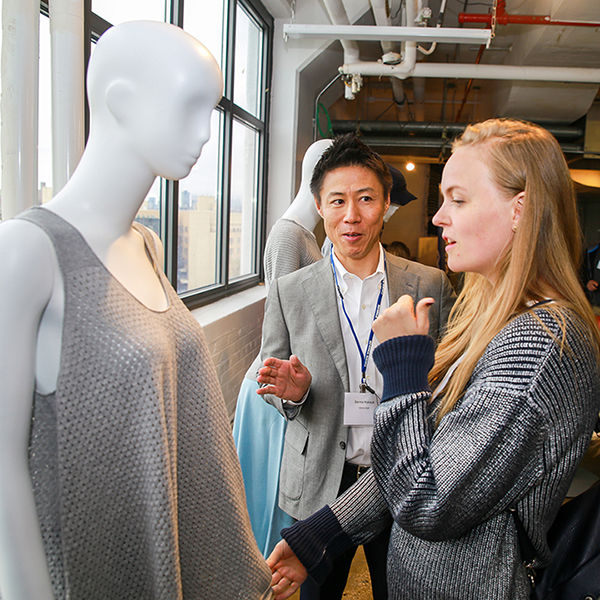
Seiichi “Senna” Nakaya, president of Shima Seiki USA, explains WHOLEGARMENT technology to an attendee.

Brooklyn Fashion + Design Accelerator (BF+DA), a collaborative space for ethical fashion, hosted the event.
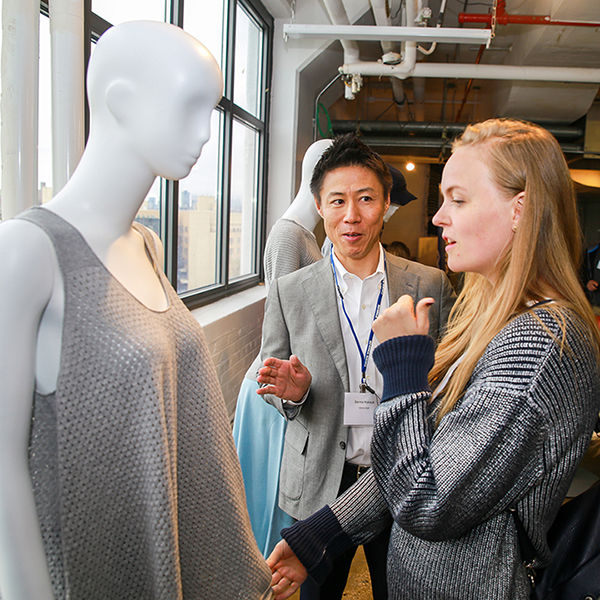
Seiichi “Senna” Nakaya, president of Shima Seiki USA, explains WHOLEGARMENT technology to an attendee.
![]() |
---|
![]() |
![]() |
![]() |
![]() |
![]() |
![]() |
![]() |
![]() |
![]() |
![]() |
![]() |
![]() |
![]() |
![]() |
![]() |
![]() |
![]() |
![]() |
![]() |
![]() |
![]() |
![]() |
![]() |
![]() |
![]() |
![]() |
![]() |
![]() |
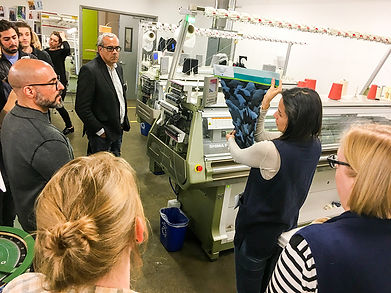

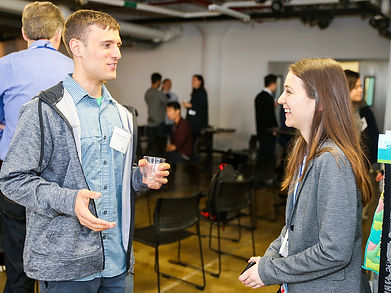

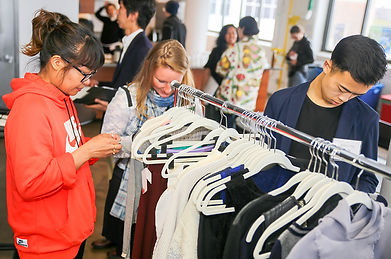


Attendees tour the BF+DA knitting lab.
Brian Hamilton of Reebock chats with Carter Jones of Shima Seiki USA.
Attendees check out garments knitted on Shima Seiki WHOLEGARMENT machines.
BF+DA students learn weaving on an old-fashioned loom in the design center.
Dr. Andre West of N.C. State is flanked by Shari Litow (L) of Honeywell and Emily Hung of Shima Seiki USA.
Sam Ming (R) of Shima Seiki USA explains some of the technologies behind these knitted garments to an attendee.
Robert Gordon of National Spinning talks with Luis Kim and his daughter Andrea Kim of BKG Knits, Los Angeles.