
Posted May 25, 2017
ÜBACH-PALENBERG, Germany – The 2.5-millionth Schlafhorst Autoconer winding unit was put into operation this year.
This record, unmatched in the sector, is another milestone in Schlafhorst’s successful company history and shows how much trust the textile industry has in its technological leadership. For over half a century, the German textile machinery manufacturer has been determining the technical and technological progress in package winding with the Autoconer.
The synonym for automatic package winding for 55 years
With the mass production of the Autoconer in 1962, the era of automatic package winding began. The sales success was staggering. As early as the preview three years prior at the ITMA in Milan in 1959, the revolutionary concept of the Autoconer sparked enthusiasm among the experts in the textile industry. Since then, the name Autoconer has been the synonym for automatic package winding.
Today, Autoconer packages are still the global benchmark for quality and efficiency.
The history of the Autoconer is characterized by a long list of groundbreaking inventions that have always increased customer benefits. Every product generation of the Autoconer exceeded the industry’s expectations regarding efficiency and technology. Revolutionary splicing technology, innovative sensor technology and control systems, the unique FX technologies and intelligent automation systems became state of the art, thanks to Schlafhorst.
Autoconer 107 – the dawn of automation
The first product generation of the Autoconer radically changed workflows in the package winding sector. In manual winding, staff had to change the tubes and provide each bobbin individually, find the upper and lower yarn end, knot them together and put it in the yarn path. Moreover, the packages had to be changed by hand.
The many manual handlings in the machine limited productivity and quality. The Autoconer 107 broke these shackles. The circular magazine with automatic bobbin changing drastically improved its ease of use. A mechanical yarn clearer, a knotting aggregate and lastly the package doffer automated the winding process. The operators were relieved of almost all manual work, thanks to the Autoconer and took on mainly supervisory functions.
Automation was the necessary prerequisite to increase productivity and quality, as the limiting factors of staff, and therefore the necessary manual interference, would be removed. Through this, the package-winding sector became significantly more efficient; it was the breakthrough that changed the labor-intensive winding process to an automatic one.
The benefits of the Autoconer 107 compared to a manual winding machine spoke for themselves:
-
The manual effort per kilogram was reduced to 1⁄4 of the previous expenditure that was required;· Production increased fourfold; and
-
The manufacturing costs per kilogram of yarn (for example Nm 34) decreased by 40 percent.
Autoconer 138 – the invention of splicing technology
The Autoconer 107 was produced for more than 15 years. Its successor, the Autoconer 138, astounded the textile world in 1976 with its separate mechanical, electric and pneumatic functions. But the real sensation entered the market only two years later.
In 1978, the innovative splicer mechanism revolutionized yarn joining: the splice replaced knots for the first time. In doing so, quality for subsequent processes was redefined. While knots were three to four times thicker than the yarn and often led to yarn breaks in knitting and weaving, the splice by Schlafhorst was practically similar to the yarn. Efficiency in processing increased considerably and the quality of the finished articles was enormously improved.
Autoconer 238 – the material flow revolution
In 1987, Schlafhorst brought the Autoconer 238 onto the market, the first winding machine with single winding unit drive. This led to increased flexibility and quality in the spinning mills. In the ‘80s and ‘90s, the increase in profitability in spinning mills was closely linked with the increasing automation of the process cycles. In 1991, Schlafhorst went on to develop the revolutionary Caddy transport system to market readiness. Spinning mills were able to use it to implement more efficient material flow and automatization strategies.
Autoconer 338 – the trailblazer for innovations in textile technology
The next product generation, the Autoconer 338, with new drives and sensors went into production in 1997, while the starting pistol also sounded for the development of intelligent FX technologies. This made Schlafhorst the trailblazer for innovations in textile technology. Autotense FX, the first online yarn tension control, is still the undisputed industry benchmark today.
Autoconer 5 – drumless yarn displacement
In 2007, Schlafhorst introduced the textile industry to the world of digital yarn displacement for processing bobbins. The Autoconer 5 revolutionized the production of process-optimized packages with its drumless yarn displacement system PreciFX.
Two years later, Schlafhorst was once again at the cutting edge of the automatization trend with the Autoconer X5. Intelligent material flow technologies, smart package handling with the X-Change doffer and flexible process optimisation with the Autoconer types RM, D, T and V allowed each spinning mill to have an individual automation concept.
Autoconer 6 – self-optimizing and E3 certified
The next major leap came in 2015. With the Autoconer 6, Schlafhorst presented an automatic package winder with self-optimized process cycles. Maximum productivity, the greatest possible energy efficiency and the absolute best quality are possible, practically at the touch of a button. As a result, the newest product generation is E3 certified because it gives spinning mills the world over threefold added value in the fields of energy, economics and ergonomics.
Success in the hotspots of automatization
In its 55-year history, the Autoconer has always celebrated its success at the hotspots of the textile industry. The first Autoconer generations were primarily sold in Europe and North America where the demand for automation of the textile industry was already quite advanced. Today, the strongest key markets are in Asia. Schlafhorst presented the 2.5-millionth milestone winding unit to the Indian textile company Kanchan India Ltd at the INDIA ITME 2016.
Commodity spinning mills and specialists across the globe are still optimizing their value chain this day with the Autoconer.
“The Autoconer shaped the industry’s history”, said the Schlafhorst product manager responsible, Peter Gölden. “Spinning mills have chosen an Autoconer winding unit 2.5 million times. To grasp that in numbers: the productivity potential behind that allows to process the production of more than 100 million ring spinning spindles! This unique trust is a major incentive for us to continue to sustainably shape the technical progress in the package winding sector with pioneering innovations in future.”
Source: Saurer Schlafhorst
Schlafhorst’s 2.5 millionth Autoconer winding unit put into operation
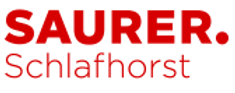

Autoconer 107
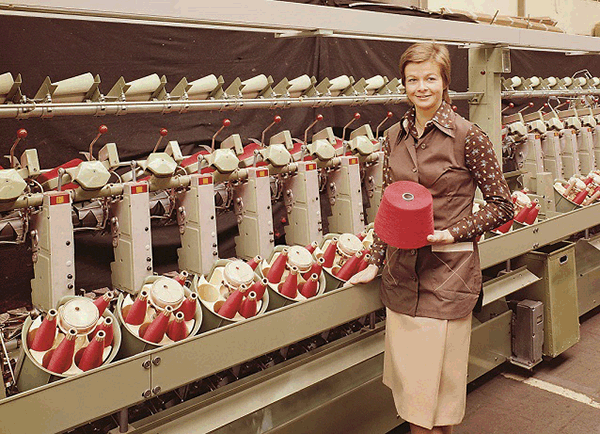
Autoconer 138

Autoconer 338

Autoconer 107