

Jim Chesnutt, who joined the textile industry in 1973 after spending 10 years in banking, provided a considered look at the industry’s and his company’s evolution based on his experience, longtime industry advocacy and first-hand knowledge.
The industry was “booming” into the 1980s before “things began to happen” that would dramatically change the face of U.S. textile manufacturing, said Chesnutt, chairman & CEO of National Spinning Co., Washington, N.C.
He went through a number of legislative matters and trade agreements, starting with President Reagan’s 1988 veto of a bill that would restrict textile imports. The industry was unified when it went to Washington, D.C., to lobby for the bill and was stunned by the veto, he said.
“That was the beginning of all of us realizing that things had to change,” Chesnutt said. “But it was not too difficult at the time. We survived – and then the Uruguay Round happened.”
The Uruguay Round of 1994, of course, phased out textile quotas over a 10-year period. And that same year, NAFTA was implemented – and that was the first U.S. trade agreement with a low-cost country (Mexico), he pointed out.
“When quotas went away, it really began to cause difficulty with the apparel manufacturers and throughout the supply chain,” Chesnutt said. “And with NAFTA, the industry warned that there would be huge job losses. NAFTA was the big wake-up call – close by, maquiladoras across the border of U.S. and Mexico, and very convenient for the importers and the retailers.”
China then began to demand concessions, and in 2001 it was allowed to join the WTO to gain full access to benefits and was also granted permanent Normal Trade Relations (NTR) status.
“Foreign policy had a lot to do with what was in trade agreements then, and we lost hundreds of thousands of jobs,” Chesnutt said. “But at the same time that those jobs were going away, automation was beginning to take place. This industry began to invest again even in difficult times because either we had to do it or it would’ve been lights out – and it was lights out for a lot of companies.”
In 2006, Vietnam was granted NTR status and became a WTO member the next year. A decade later, in 2016, Vietnam shipped $11.3 billion in textiles and apparel to the U.S., he pointed out.
“China is not who we need to be concerned about in the textile and apparel business today,” Chesnutt said. “It’s Vietnam. However, I think we’ve moved beyond that. I imagine most of you in this room today are doing things that you didn’t dream of doing 15 years ago or 10 years ago – or how about five years ago?
“Who would’ve ever thought that National Spinning Co. would’ve been selling yarn for $51 dollars and change per pound?” he continued. “It’s different – it’s military, it’s technical. And that’s what most of us are doing in this room now, something different. Everything has changed, and it’s changed because of market demands and consumer demands, and this industry has reacted positively to those changes.”
CAFTA was approved by Congress in 2005, and that has been a plus for the U.S. textile industry due to yarn-forward rules and duty-free language, Chesnutt said. Last year, the U.S. exported $3.1 billion in textile goods to CAFTA countries and imported $8.2 billion in product (many containing U.S. textile components) back from that region.
“I don’t think there’s a person here in this room today who would want to eliminate CAFTA and/or NAFTA, because what we have sent out and the number of jobs that are created due to those exports is so very important to us,” he said.
Chesnutt also covered the Korea-U.S. free trade agreement (KORUS) and the now-dormant Trans-Pacific Partnership (TPP), the latter of which he called a “big loser” for the U.S. textile industry.
“We have to be better,” he said. “We have to be in a position to deliver fast, we can deliver efficiently and we can deliver products that meet the needs of customers that need them so much.”
Going forward, Chesnutt said that multilateral agreements might be a thing of the past, given President Trump’s opposition to multi-country free trade deals. Bilateral agreements will probably the norm for the foreseeable future, he said.
“I will say this about going to Washington, D.C., two weeks ago (for the National Council of Textile Organizations’ Annual Meeting),” he said, “and I’ve been going there for 35 years: It’s the first time I ever went there and Capitol Hill felt positive about our industry, and we were not going to Washington to try to stop a threat. For me, that’s a positive for everyone in this room – that we worked our way back into a position of respect in Washington, because of the fact that we’ve been able to create more jobs, we’ve been flexible and we’ve been able to meet customers’ demands. And I think that’s going to be very positive in the future.
“We’ve seen the models in the retail trade today: fast replenishment, quick turns, reduced inventories,” he continued. “It’s absolutely going to happen and there’s only one industry that can do it in this country and do it efficiently, and that’s the U.S. textile industry.”
Chesnutt later dove into the numbers related to the value of textile shipments, exports, capital investment and employment figures before explaining how his company has changed and survived.
Traditionally a spinner and dyer of acrylic and wool yarns for hosiery, sweater, upholstery and craft yarns, National Spinning Co. has evolved into a spinner and dyer of specialty fibers, including moisture management polyesters, recycled fibers and fire-resistant blends for protective apparel and industrial products, he said.
“The only way we could cope and be successful was to change,” he said. “And as I look around here today and see a lot of people that I’ve known for a long time, the reason we’re still here today is because we have changed and innovated and leaned on N.C. State when we’ve needed to – and, we’ve begun to find that we can get new people to work for us.”
Chesnutt has witnessed industry’s demise, rebirth
STA Northern Division meeting
Industry's resilience reiterated at N.C. State
Posted May 3, 2017
Stories by Devin Steele (DSteele@eTextileCommunications.com)
RALEIGH, N.C. – “Resilience” was a key, one-word takeaway that emerged from the Southern Textile Association’s (STA) Northern Division Spring Meeting at N.C. State’s College of Textiles (COT) here last month.
Not to mention “undying.” And probably “thriving.”
What other words could come to mind for the 90-plus attendees of the event after speakers spent a half day obliterating the notion that the textile industry is dead?
From a dissemination of the multitudinous activities at NCSU’s College of Textiles; to a personal testimony from one of the industry’s esteemed leaders; to an overview of a high-tech, innovative process in which an industry supplier is involved; to a well-cited economist heaping praise on the industry – presenters put a giant exclamation point on the current state of affairs – and a bright future – for U.S. textiles.
To that end, an industry “outsider” provided the day’s money quote:
“I want to let you know how impressed this economist is with what you have been doing as an industry and what the College of Textiles has been doing in terms of taking an industry that was probably written off and transforming it,” Michael L. Walden, William Neal Reynolds Distinguished Professor and Extension Economist at NCSU, said in closing his presentation. “You are hard-pressed to find an industry in the United States that has had more forces imposed on it than the textile and apparel industry and you have positively responded and are remaking the industry. So you all deserve your own applause.”
From an insider’s perspective, next speaker Jim Chesnutt, chairman and CEO of National Spinning Co., Washington, N.C., reiterated Walden’s conclusion:
“Even under the threat that we’ve been under, the resilience of this industry has proven itself over and over again under tough circumstances,” he said, after explaining how his company was forced to evolve in order to survive over the last two decades.
In that same vein, to underscore the day’s unwritten theme, Kent Hester, director of Student and Career Services at the College of Textiles, titled his presentation, “Dispelling the Myth of a Dying Textile Industry,” and presented a good argument to support that declaration. And changing minds is a battle in which he has been engaged for more than three decades, he said.
“When I graduated high school in 1985 and told everybody I was applying to State for textiles, they all told me, ‘why would you go into textiles? It’s a dying industry.’ And that was back during some better times than we’ve seen since then,” he said. “Even then, as you know, textiles was a canary industry. The textile industry has always been one of those indicator industries – we’re the first into a recession and we’re usually one of the first to come out. And we’ve been very proud of that because every time, we’ve come out of those recessions. We always change, we’re always different, we emerge in a lot of variations, but we’ve always come out.”
Sure, extolling the virtues of the U.S. textile industry was preaching to the choir with this group of yarn, fabric, machinery and supply makers and merchants. But the STA did count among attendees several textile students who may have left with a better feeling about their chosen major – not to mention an economics professor from UNC-Chapel Hill who weeks earlier had written in The News & Observer of Raleigh that the industry was “all but gone” – but came away with a different opinion after the meeting.
Deeply embedded perceptions of the industry are difficult to change, of course, and David Hinks, dean of the College of Textiles, addressed that issue during a Q&A session.
“One area that I think is really important is for us to think about is reimagining manufacturing in the United States, and textile manufacturing in particular,” he said. “We have a marketing budget that is pretty limited, so we can’t change the image of textile manufacturing by ourselves. But I think together, collectively, we can start that process.”
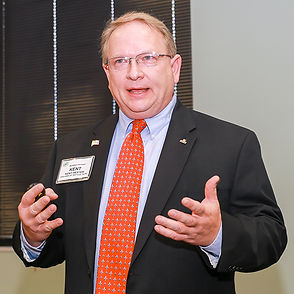
Death of industry greatly exaggerated
In addressing the title of his presentation, Kent Hester, director of Student and Career Services at NCSU’s College of Textiles, asked ‘how do you measure “life” in the textile industry? Is it by number of fiber, yarn and fabric mills? The number of dyeing and finishing mills? The number of nonwovens/engineered fabrics facilities? The number of employees? By productivity? Sales dollars? Or by percentage of GDP?
“Today, I’m going to get you to think a little differently about ways that we measure not only the life of the industry but also what is the textile industry,” Hester said. “How do you define the textile industry?”
He then went on to cite a number of facts and figures that speak to the health of the industry. Among U.S. manufacturing industries, he said, textiles rank near the top in productivity increases. Automation and the closure of inefficient plants is the primary reason, he added.
He also pointed out that the industry is a key contributor to national defense as it supplies more than 8,000 products to the U.S. military per year. Also, the sector invested $1.96 billion last year, he added.
In addition to rising capital investments and profits and better use of technology and metrics, reasons for optimism are aplenty, Hester said. Among them: a renewed interest in and support of U.S. manufacturing; the possible closing of trade agreement loopholes; proposed moves against currency manipulation; Buy American campaigns; more innovation and improved marketing strategies; some slowdown in imports and a slowdown of major job losses; and a more skilled workforce.
“Will it ever get to where it was, say, pre-2008, in the heyday?” he asked. “I don’t think it will and I don’t think it should because I remember working for plants where there was probably a lot of mismanagement and inefficiencies. There were a lot of things that probably shouldn’t have gone on because we were fat and happy back then. And we survived and got through the ups and downs. But now those margins are a lot smaller, so you can’t afford to rest on your laurels.”
Hester then asked: How do we define the U.S. textile industry? He followed with a series of thought-starters to answer that question.
“Is it just fiber and fabric mills, or just dyeing and finishing mills?” he asked. “Is it nonwovens? Or, should it be defined more broadly? Is it U.S. companies only? How do we count those foreign companies that have started textile manufacturing operations here? Are those considered U.S. companies? Are they international companies? What happens when they export things back to their countries? Are they U.S. exports?
“It muddies the water when you start to see all those different variations that we’ve never seen before,” he added.
Now, Hester said, the College of Textiles places graduates in many companies that aren’t considered part of the textile industry, when purely defined. Among them: medical, military, construction, aerospace, signs and banners, hospitality, transportation/automotive, marine, safety, consumer products, aeronautical, protection, fashion and athletic/sportswear.
Hester then discussed employment placement rates among COT graduates, starting salaries, internships, partner companies and more, before closing with challenges ahead.
Those challenges include:
-
Rebranding the industry. “We have trouble filling enrollment sometimes because Millennials may not want to go into manufacturing,” he said. “But when we take them to a textile plant now, their eyes are wide open.”
-
Losing experience and knowledge to retirement. “Once, twice, three times a week I get a call from someone in the industry saying that their top technical person will be retiring and they don’t have anybody in the pipeline. For 10, 15, 20 years, people weren’t hiring into manufacturing in large numbers.”
-
Finding a qualified workforce to fill the void. “I’m going to encourage some of you to start looking at our graduate students, our master’s and Ph.D. students and some of our international students. The majority of our graduate students are international. They come here, we educate them and then our companies won’t hire them because they have to sponsor them. So they go back to their own country and compete against you. Maybe you should consider changing that philosophy, if you can.”
-
Attracting and keeping that talent. “That onboarding and training is a little bit different now than it was 10 or 15 years ago, so we need to think about that.”
'How do you define textiles?' asked Kent Hester, director of Student and Career students at N.C. State's College of Textiles. 'Is it just fiber and fabric mills, or just dyeing and finishing mills?” he asked. “Is it nonwovens? Or, should it be defined more broadly? Is it U.S. companies only? How do we count those foreign companies that have started textile manufacturing operations here? Are those considered U.S. companies? Are they international companies? What happens when they export things back to their countries? Are they U.S. exports?

College of Textiles ‘firing on all cylinders’
During his presentation, David Hinks, dean of NCSU's College of Textiles, provided a snapshot of all the exciting things happening at the College, noting that 140 faculty and staff serve about 1,000 undergraduate students and 235 graduate students and adding that the College counts some 400 industry partners. Faculty, staff and student impact in the 2015-16 academic year was $14 million in research and testing funding; 160 companies and eight government agencies; 25 patents/disclosures; and 160 publications and juried exhibitions.
On enrollment, Hinks said, “We’ve yo-yoed over the years for various reasons but what’s happened over the last 10 years is tremendous growth. We’ve revised our curriculum to be more innovative, to be more serving of the industry and to be broader and more flexible. So we’re now near our 2025 targets for Ph.D., master’s and Bachelor of Science degrees. So there’s never been a time that we’ve been stronger, in my view. In fact, we’re in a mode of enrollment management over growth.”
Hinks also discussed how the College’s educational programs serve the entire textiles enterprise, from polymer and color chemistry to textile technology to textile engineering to fashion and textile design/management.
“We’re really firing on all cylinders,” he said.
Later, Hinks talked about the convergence of two disruptive drivers – global textile industry innovation and higher education innovation – and the unique opportunity this provides.
“This is a time of significant disruption in the textile industry,” he said. “We’re seeing a tremendous investment in this region, and there is an interesting local-for-local movement, manufacturing locally to the market. There’s a need for fashion innovation and there’s a need for new fibers and fabric constructions and new materials.
“At the same time,” he continued, “there’s a disruption in higher education. We’re looking at different learning styles, different learning technologies, blending online content with in-class and laboratory and production facilities. And cost is an issue: How do we provide great access to students and improve the quality at a reasonable cost per family? And we take that very seriously. We’re serving the entire textile enterprise and, in my view, our College is the only textile school that really can serve these new disruptive environments – higher education and serving our industry at the same time.”
'There’s never been a time that we’ve been stronger, in my view,' said David Hinks, dean of N.C. State's College of Textiles. 'In fact, we’re in a mode of enrollment management over growth.'
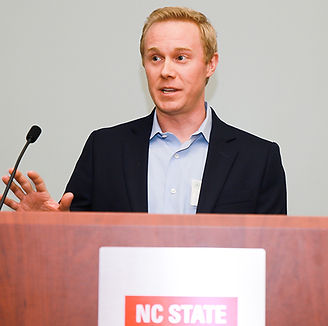
Wade Tyner, manager of Applications Engineering at APJeT®, Morrisville, N.C., offered a look into the high-tech world of textile manufacturing. APJeT is a unique company that uses atmospheric plasma technology to change and enhance the surface properties of a wide variety of materials, beginning with but not limited to textiles.
Plasma, he explained, is the fourth state of matter that includes solid, liquid and gas. Plasma is a highly energetic, ionized matter that contains ions, electrons, neutrons, photons and free radicals. It has nearly zero net charge, yet is electrically conductive that can be generated and manipulated by various electrical means, he said.
Tyner added that plasma can be used to remove substances through cleaning or etching; modify a substrate through substrate activation or functionalization; and deposit chemical materials (i.e. finishing textiles) through grafting or chemical finishing.
Using plasma in manufacturing applications has several key benefits, he pointed out, including: it is sustainable (no water usage, is a non-thermal process and consumes lower energy and chemicals); is aesthetic (no change in chemical properties and has the ability to treat sensitive materials); and has a smaller footprint.
Tyner also discussed APJeT equipment and various commercial plasma categories for finishing and pre-treatment, before delving into APJeT’s patented finishing technology such as durable water repellence; antimicrobial, moisture management, flame resistance and color.
APJet equipment is manufactured by Morrison Textile Machinery of Fort Lawn, S.C., Tyner said. Its president, Jay White, serves on the APJeT board and attended the STA meeting.
APJeT®: A leader in plasma technology
![]() |
---|
![]() |
![]() |
![]() |
![]() |
'I imagine most of you in this room today are doing things that you didn’t dream of doing 15 years ago or 10 years ago – or how about five years ago?' said Jim Chesnutt, chairman and CEO of National Spinning Co.