
Posted April 2, 2020
By John McCurry
The textile and apparel sector is answering the call to produce masks and other personal protective equipment (PPE) to assist the medical community’s battle against the coronavirus.
Dozens of companies are now involved in one way or another. Some are part of a consortium led by Parkdale Mills. Others are undertaking efforts on their own, or partnering with other firms on a smaller scale.
Following is a look at the efforts of three companies that began production within the last few weeks.
America Knits
America Knits is a relatively new cut-and-sew operation that began operations last July in Swainsboro, Ga., about 90 miles west of Savannah. Co-owner Steve Hawkins picked the location to manufacture products including T-shirts and undergarments, but had no idea that nine months later he would be shifting all of his production to fill a need in times of a national crisis.
America Knits’ 70 employees began producing masks on Monday and manufacturing has gradually ramped up. At first, the effort worked out some kinks, but Hawkins said production is on a good curve now. The company is converting 80 percent of its production to make FDA-approved three-ply masks and the remaining 20 percent for hospital gowns.
“We spoke with our current customers when all of this started last week and completely retooled the plant to produce these much-needed masks,” Hawkins said. “We are committed to produce 1.5 million masks over the next 12 weeks.”
America Knits has a federal government guarantee to purchase 12 weeks of production, but Hawkins said his company may continue making healthcare products on an ongoing basis.
“There is definitely a market for U.S.-made products in healthcare,” he said.
America Knits’ first shipments will leave the factory next week and Hawkins said he expects to be shipping daily to FEMA distribution centers.
Hawkins said he is requiring employees to wear the masks they manufacture. Also, someone takes their temperature each day. So far, no one has tested positive for COVID-19.
“Most important, we start each day with a prayer and ask God to protect and look over our factory as we undertake the massive need,” Hawkins said.
Spoonflower
Spoonflower, a Durham, N.C.-based digital printer, is bringing color to the mask manufacturing effort. The company is making a gaiter-style mask and a double-layer fabric mask. Both have undergone an iterative process since the prototypes were launched on March 21.
The company’s focus is on making non-medical grade fabric masks to help address the global shortage. Spoonflower said the medical community plans to use their masks as an added layer of coverage to extend the life of the N95 masks and potentially augmenting other masks.
Michael Jones, Spoonflower’s CEO, said his company was able to pivot its manufacturing and operation workflows. The company’s location, in the midst of a nexus of healthcare academics and manufacturing, proved to be fruitful, with Duke University, the University of North Carolina at Chapel Hill and WakeMed Health and UNC Rex Hospital nearby.
“Though this proximity and partnership, we were able to receive early feedback and guidance from these local healthcare professionals who shared their needs for comfortable longevity of wear, breathability and fit,” Jones said. “As an on-demand manufacturing facility, we have the flexibility to make modifications in real-time and will continue to do so as we receive more feedback from those on the frontlines.”
Spoonflower also has a community of 4.5 million creatives and makers who have been very vocal about wanting to support its efforts, Jones said. On March 30th, the company launched its program to provide a special fabric at roughly cost to support their mask-making efforts for their local community. Spoonflower also made its templates available to this community.
“We have optimized our print-on-demand capabilities for this fabric, so when someone orders it for mask-making, they can maximize the number of masks, which also limits waste fabric,” he says. “Our goal here is to get as many masks as possible from a yard of fabric. Right now that is around 12 masks.
“We’ve transformed our print operations and cut-and-sew facility to support this initiative. Leveraging our proprietary textile technology, we can ensure that fabric printed for mask-making is optimized to produce the largest number of masks per yard while minimizing waste and offers the template printed directly on the fabric.”
To enable social distancing, Spoonflower relocated its sewing team into its office, since its office staff has been working from home since March 18.
Jones said Spoonflower is ramping up production daily as it begins to allocate more resources.
“We know the greatest asset we have is our global community of 4.5 million makers,” Jones said. “Mobilizing this passionate and talented group of people will be key to get masks into as many hands as possible. Since the program launched on March 30th, 715 yards have been purchased by our community for mask making which equates to an estimated 8,580 masks, and this number grows by the day.”
Spoonflower is ramping up production daily as it begins to allocate more resources to this effort.
Spoonflower also put a call out to its 220 employees to help with sewing and donated what minimal scrap, or flawed in production fabric, it has to support their efforts.
Jones said it’s eye-opening to hear directly from those in need. Spoonflower has requests for more than 5,000 masks and the numbers grow every day.
“We receive emails from nurses who have lost co-workers to COVID-19 because they don’t have the right equipment,” he said. “Doctors are intubating patients without any protection. Hearing these stories fuels us every day and we hope others will continue to join us in this mission to get equipment into the hands of our brave healthcare workers.”
Greenwood Mills
Greenwood Mills, Greenwood, S.C., is producing face masks and gowns for non-medical use in hospitals, nursing homes and other facilities. The face mask is two plies of a 65/35 polyester/cotton twill with a 100 percent polyester fusible lining holding them together. The gown is made on one ply of the 65/35 with a water-repellent application.
“In normal circumstances, we are working with belt loop, rivet machines and double-needle machines to produce our denim garments,” said Greenwood President Jay Self. “However, to make this PPE, our team has shifted production to our single-needle machines, of which they are all trained to use.”
Self said the company’s first week of production will result in about 30,000 masks. At full capacity, it will have the ability to produce 500,000 masks and 300,000 gowns per week, with flexibility depending on the demand of the products.
“Greenwood Mills has been weaving fabrics for more than 125 years and has been supported by our community for just as long,” Self said. “Now, when our community is most in need, we knew we had a responsibility to help. We are glad to be a part of the solution to ensuring those on the frontlines of this health crisis have what they need to stay safe and healthy, so they can serve the most vulnerable.”
Self said Greenwood is fortunate that its corporate offices were designed to give each person a private work area, which allows for social distancing. At its factory, Greenwood is spreading out machines, creating distance between workers, he added.
STEPPING UP
America Knits, Spoonflower, Greenwood Mills among textile companies answering nation's call for PPE production

Face masks are sewn at America Knits.
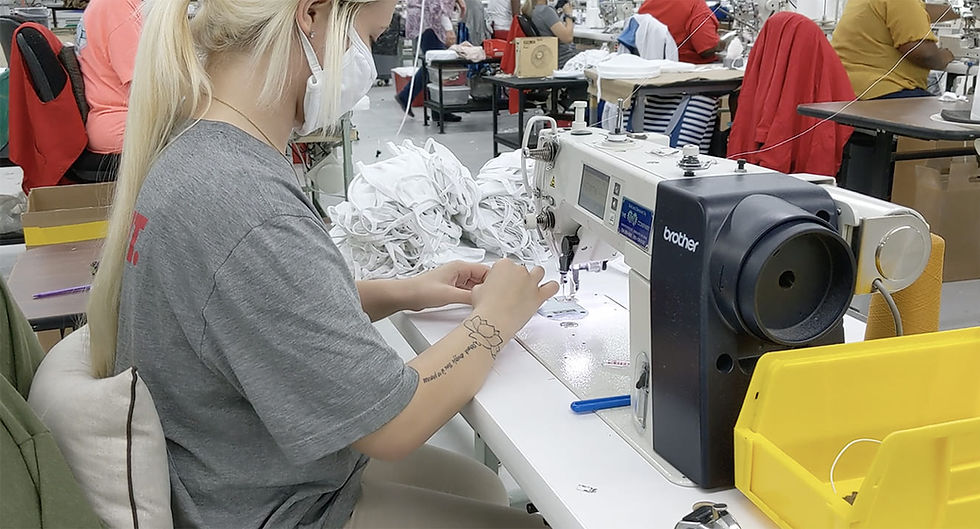
Face masks are sewn at America Knits.

An isolation face mask made at Greenwood Mills

Face masks are sewn at America Knits.