
The combination of these technologies reduces the use of water and chemicals by 90 percent and energy consumption by 50 percent, according to Jeanologia CEO Enrique Silla. Additionally, he added, the technology recycles 100 percent of the water it does use, eliminating the need for water treatment and also the use of pumice stone, which produces unhealthy dust particles and requires several post-production washings.
“This represents a revolution in the textile industry,” Silla told eTC during ITMA. “Jeanologia has transformed the way that jeans are produced, by way of technologies that reduce the use of water, chemicals and energy, and we are now taking this transformation a step further with our ZERØ® technology.”
Most encouraging with this technology, perhaps, is it completely eliminates potentially harmful practices such as sandblasting, manual scraping, stonewashing and permanganate potassium spraying – processes that have been widely rebuked by a number of global ethical issues groups and have actually been banned by a number of global denim brands.
“Jeanologia is helping to improve transparency in the textile industry, which at times has been accused of archaic and pollutant production processes,” Silla said. “The technological innovation provided by The Zero Discharge Production Center is key when it comes to certifying an industry as sustainable.”
Archroma, Patagonia team up
Another industry supplier that is actively participating in the “green” jeans movement is Archroma, a global color and specialty chemicals producer. The Reinach, Switzerland-based firm has developed an ADVANCED DENIM concept, which it said is a state-of-the-art, whole product concept design that “seamlessly unites technology, ecology and fashion in a single, sustainable package.”
Posted January 6, 2016
By Devin Steele (DSteele@eTextileCommunications.com)
MILAN – Consumers worldwide have had an undying love of jeans – especially, over the last two decades at least, those with a distressed or already-worn look. But creating that popular effect – and producing denim in general – has typically been a dirty and potentially unsafe process.
But in this era of sustainability, a number of companies have worked diligently in recent years to improve denim finishing techniques, which historically require high water and energy usage as well as polluting and hazardous chemicals. As a result, incredible strides to reduce the ecological footprint and raise health and safety processes of denim production have been made.
One of those companies, Jeanologia of Valencia, Spain, recently introduced its latest innovation in the area of sustainable technologies at ITMA in Milan. The 22-year-old, family-owned company demonstrated what it calls The Zero Discharge Production Center, which it said is the first denim treatment plant that “guarantees zero contamination or waste.” To achieve this, the center combines three technologies it has developed over the years: a laser, which is used to create a vintage effect; Ozone G2, a machine that uses air to reproduce ozone gas conditions to give garments a worn look; and eFlow, a waterless system that transforms air into nanobubbles, which help produce a soft hand and reduces shrinkage. Jeanologia refers to the combined technology as “ZERØ®.
ITMA 2015
GREEN JEANS
Sustainable denim finishing techniques gaining steam


Jeanologia demonstrates technique during ITMA.

Jeanologia CEO Enrique Silla addresses the press during ITMA.
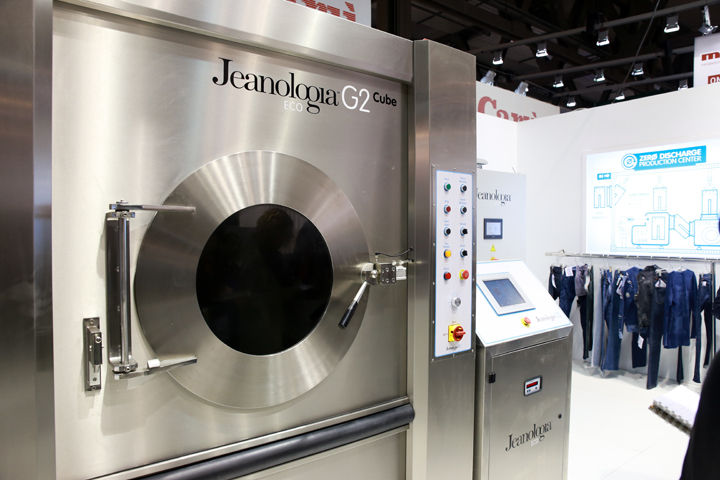
Jeanologia demonstrated what it calls The Zero Discharge Production Center during ITMA.

Jeanologia demonstrates technique during ITMA.

Valentina Politi and Domenico Luzzi are on hand in the Sei Laser booth at ITMA.

A denim display in the Sei Laser booth at ITMA

Flexi Denim safeguards the environment by reducing water consumption by 80 percent and eliminating the use of toxic chemicals.

Valentina Politi and Domenico Luzzi are on hand in the Sei Laser booth at ITMA.

In one of its latest more recent announcements in the denim finishing area, Archroma reported that its partner, clothing company Patagonia of Ventura, Calif., USA, is using a dyeing and manufacturing process developed by Archroma.
The process uses Diresul® RDT dyestuffs that bond more easily to cotton, minimizing the resource-intensive and environmentally destructive indigo dyeing, rinsing and garment washing process used to create traditional denim, according to Archroma.
As a result, Patagonia is using 84 percent less water, 30 percent less energy and emitting 25 percent less CO2 than conventional synthetic indigo denim dyeing processes, Archroma said. These dyestuffs are pre-reduced sulfur dyes with minimal sulfide content and were specifically designed to achieve the same final appearance as indigo with less waste and improved efficiency, said Julie Crowder, Brand Marketing executive, USA, Textile Specialties Business at Archroma.
“The range has been recently supplemented with new, exciting products, such as the new bright Diresul® Pacific Blue RDT, further pushing the limits of design and creation, and the Optisul® C liquid dyes that include new colors and effects with zero water dyeing consumption,” she told eTC. “Optisul® C products are affinity-free and sulfide-free dyes, and suitable for GOTS (Global Organic Textile Standard) and bluesign approval. They also allow easier application than current piece dyeing techniques for physical and chemical wash-down effects.”
In explaining how water and energy are saved and CO2 emissions are reduced, Crowder noted that dyeing blue denim traditionally involves dipping the fabric into 10 to 12 successive boxes prior to the sizing stage. But Archroma’s Denim-Ox process radically slashed this number to four, and its Pad/Sizing-Ox process reduces it yet again to just one box, she said.
“In the past, most of the features and effects that make jeans so special and so versatile have been created during wash-down using chlorine and permanganates, use of which is controversial,” she said. “Apart from eliminating hydrosulfite in the dyeing process, ADVANCED DENIM also allows the use of peroxide-based wash-downs and sidestep any environmental issues. All this means is that manufacturers and consumers who care about sustainability now have a real choice without compromising on visual effects.”
Other advancements
Among other ITMA exhibitors that demonstrated potentially game-changing technologies in the realm of sustainable, safer denim finishing practices was Sei Laser. The Curno, Italy-based company introduced Flexi Denim, a digital laser machine that can replace traditional, manual methods for discoloration, abrasion, decoration, marking, engraving and cutting of jeans and other finished garments. Flexi Denim safeguards the environment by reducing water consumption by 80 percent and eliminating the use of toxic chemicals, according to Domenico Luzzi, the company’s managing director.
“The time is right to introduce this type of technology for denim,” he told eTC during ITMA. “This is a cleaner and more natural way to create those effects.”
With “Master the Art of Sustainable Innovation” the theme of ITMA, denim finishing obviously ranked high in the area of sustainable process, as evidenced by the fact that Levi Strauss & Co. of USA was the winner of the first ITMA Sustainable Innovation Award from the European Committee of Textile Machinery Manufacturers (CEMATEX).
Levi Strauss collaborated with ITMA exhibitor Tonello of Italy to develop NoStone®, a new finishing technique that provides a mechanical alternative to pumice stones.
By using a stainless-steel abrasive drum to achieve the stonewashed effect, the system reduces water usage, production costs and carbon footprint, according to Levi Strauss.
Activists’ pressure, consumer awareness and the textile industry’s desire to “do good” have driven exponential reduction of natural resources, waste, and potentially hazardous chemicals and processes in recent years, particularly in the area of denim production. Stronger collaboration between retailers, brands, manufacturers and suppliers has led to this massive sea change toward sustainability and health and safety improvement. With such leaps being made, the outlook for denim manufacturing looks far from distressed.